Switching from Coal Slag to GMA PremiumBlast™
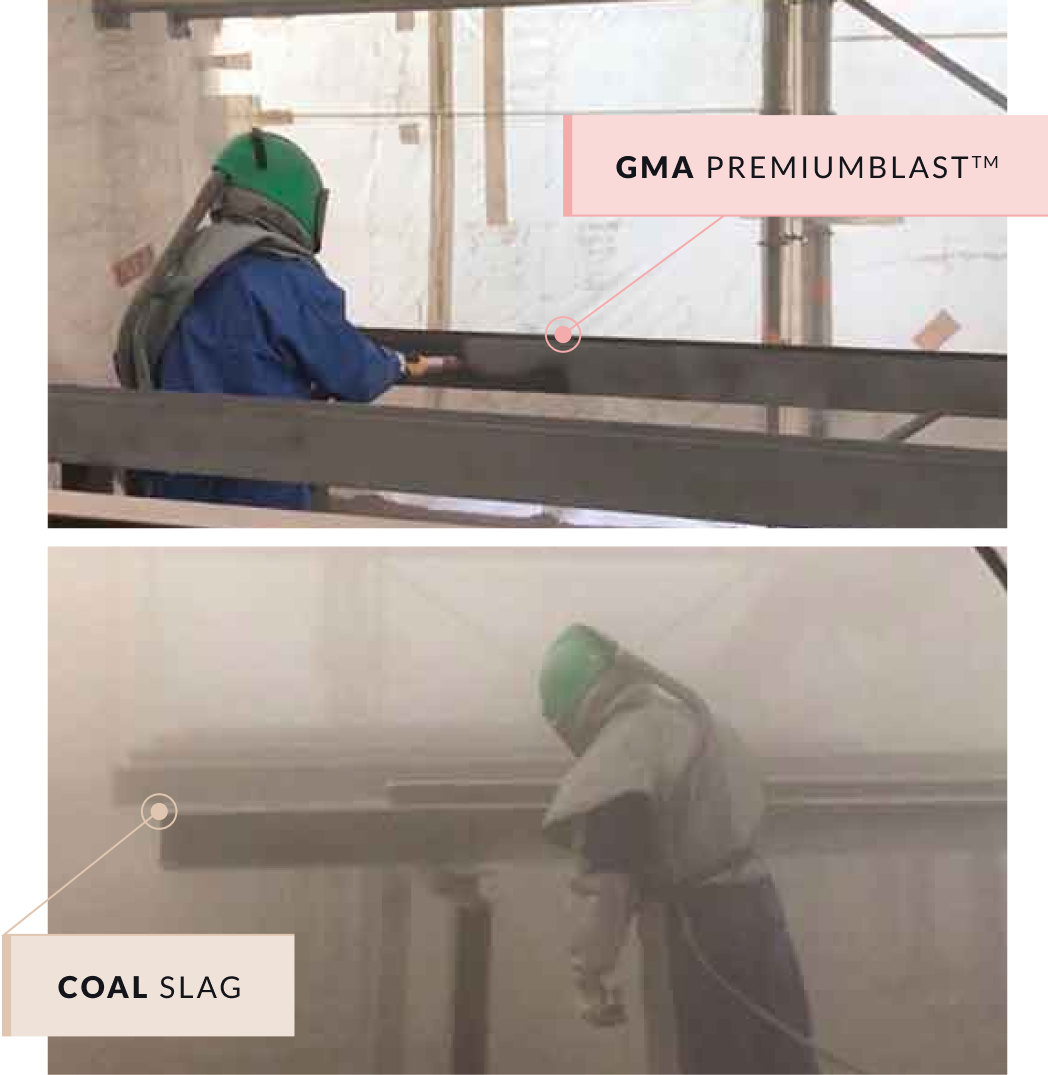
Improve working conditions across blasting sites
Cologne, Germany
Blast trial on site to test GMA PremiumBlast™ Garnet against coal slag
To improve visibility and working conditions on site
GMA PremiumBlast™ was tested on a test plate coated with 5mm lnterthem7050, 10 mm Chartek 7, and 50 μm of the base coating lnterplus 256
ZÜBLIN Chimney and Refractory (ZCR), a large industrial maintenance company was tasked with a surface preparation project that required a fast turnaround, and a focus on improved worker safety. High dust levels from traditional abrasives were causing visibility issues and excessive cleanup, resulting in productivity delays.
The key challenge the company faced was the significant dust created by their existing abrasive media. ZCR had been using coal slag for their abrasive blasting projects across Europe. As the business grew, they were looking for ways to improve the working conditions for their workers, making it as clean and safe as possible. High dust levels not only posed health and safety concerns but also reduced visibility, slowing down the overall progress of the project and requiring extensive cleanup time.
GMA PremiumBlast™ was trialed to address the issue of dust, high consumption levels of coal slag, and poor worker productivity. Known for its low dust emissions, GMA PremiumBlast™ garnet offered a cleaner and more efficient alternative to the previously used coal slag, and once the switch was made, the team immediately noticed significant reductions during blasting.
During the trial, there was a considerable reduction in dust levels, and operator visibility was greatly improved while blasting with GMA PremiumBlast™.
The blasters’ blasting techniques were evaluated, and equipment settings were finetuned. By reducing the air pressure to 7 bar, which was less tiring for the blaster, GMA was able to optimize the abrasive flow while reducing abrasive consumption.
Besides increasing the cleaning speed, especially for removing isolation coatings*, the blasted surfaces were free of embedment and other pollutants/contaminations.
GMA PremiumBlast™ successfully delivered low dust emissions, creating a cleaner and safer work environment. The reduction in dust improved visibility, reducing safety concerns, and minimized cleanup, allowing the project to be completed more efficiently. With these benefits, GMA PremiumBlast™ proved to be an effective abrasive solution and a reliable choice for future projects focused on safety and productivity.
GMA PremiumBlast™ is not available in all markets however its low dust performance is consistent with the full GMA Garnet™ blast abrasives range. Speak to your regional expert about the GMA range in your market.
*GMA PremiumBlast™ was tested on a test plate coated with 5mm lnterthem 7050, 10 mm Chartek 7 and 50 µm of the base coating lnterplus 256.
Subscribe to our e-newsletter for the latest news and events at GMA.