You’re currently viewing the Americas website.

You’re currently viewing the Americas website.
Would you like to switch countries or language?Blast Abrasives
Topics
Waterjet Cutting
Topics
Resources
Categories
Types
Categories
Topics
Waterjet Cutting Tech Tips English Global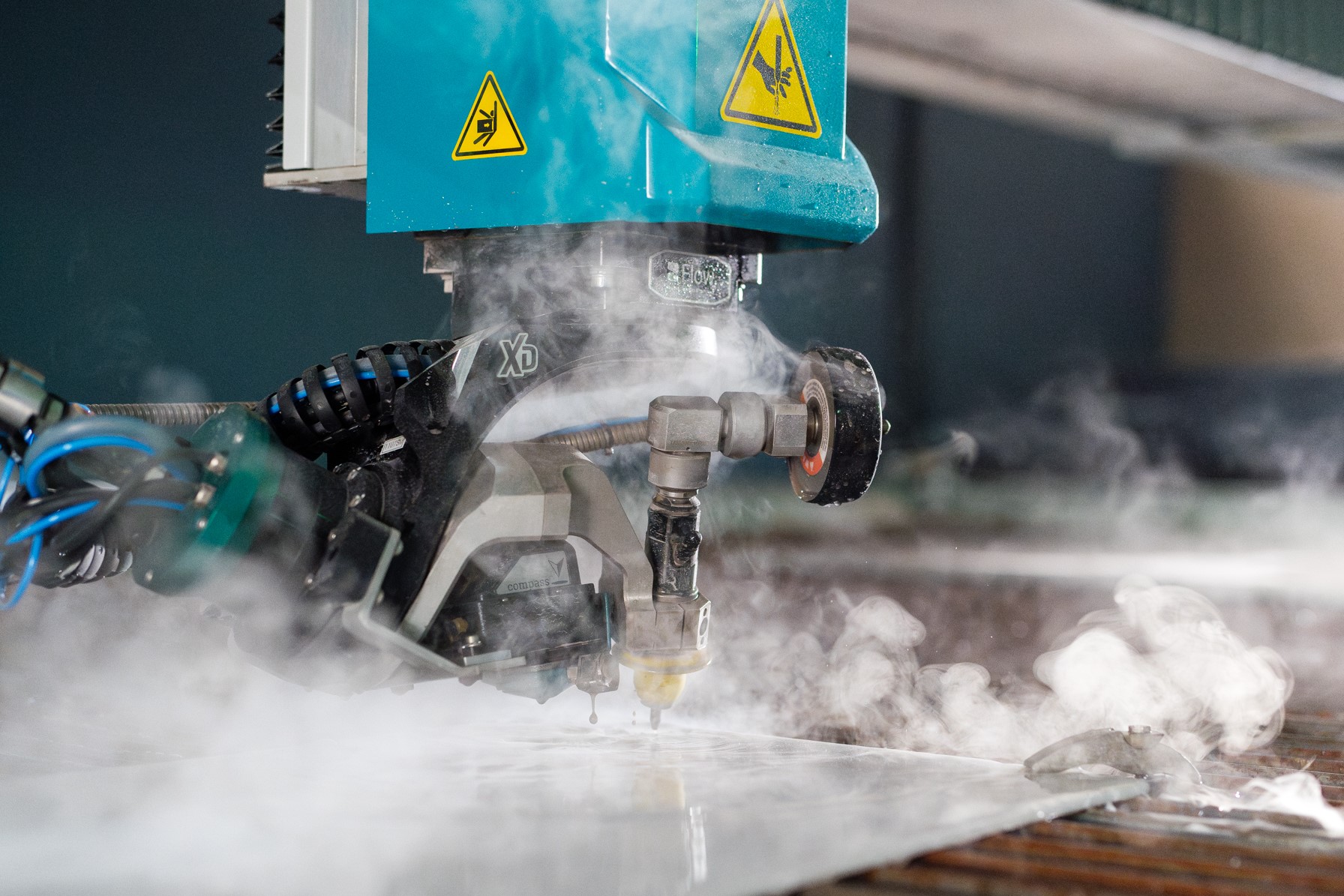
Why is Garnet the preferred abrasive in Waterjet cutting?
Garnet has become the preferred abrasive in waterjet cutting due to its ideal balance of hardness, toughness, and durability.
While softer materials like olivine may extend the life of your mixing tube, they do not match garnet's cutting speed. Conversely, harder abrasives like aluminum oxide can cut faster but often compromise the quality of the finish and drastically reduce the mixing tube's lifespan. Garnet offers the best of both worlds—efficient cutting with a high-quality finish and reduced equipment wear.
Top Tip: Choose garnet for the best balance of speed, quality, and equipment longevity.
What to Expect from a Waterjet Cutting Machine
Waterjet cutting is a highly versatile and precise method, ideal for a wide range of materials, from soft plastics to the hardest metals. Unlike laser or plasma cutting, which can cause heat-affected zones and are limited in material range, waterjet cutting leaves no thermal damage and can handle complex 3D cuts. Advanced waterjet systems can even perform simultaneous parallel cuts with multiple heads for increased
efficiency.
Top Tip: For maximum flexibility, use waterjet machines with multiple cutting heads or five-axis capabilities for complex designs.
How Garnet Quality and Delivery Impact Performance
The quality of garnet significantly influences cutting performance. High-quality garnet, such as GMA Garnet™, known for its hardness and low friability, provides consistent results, faster cutting speeds, and less wear on equipment. It’s also crucial to maintain a consistent flow of garnet into the cutting head to ensure smooth operation and high-quality cuts.
Top Tip: Opt for high-quality garnet and ensure consistent abrasive flow to enhance cutting performance and extend equipment life.