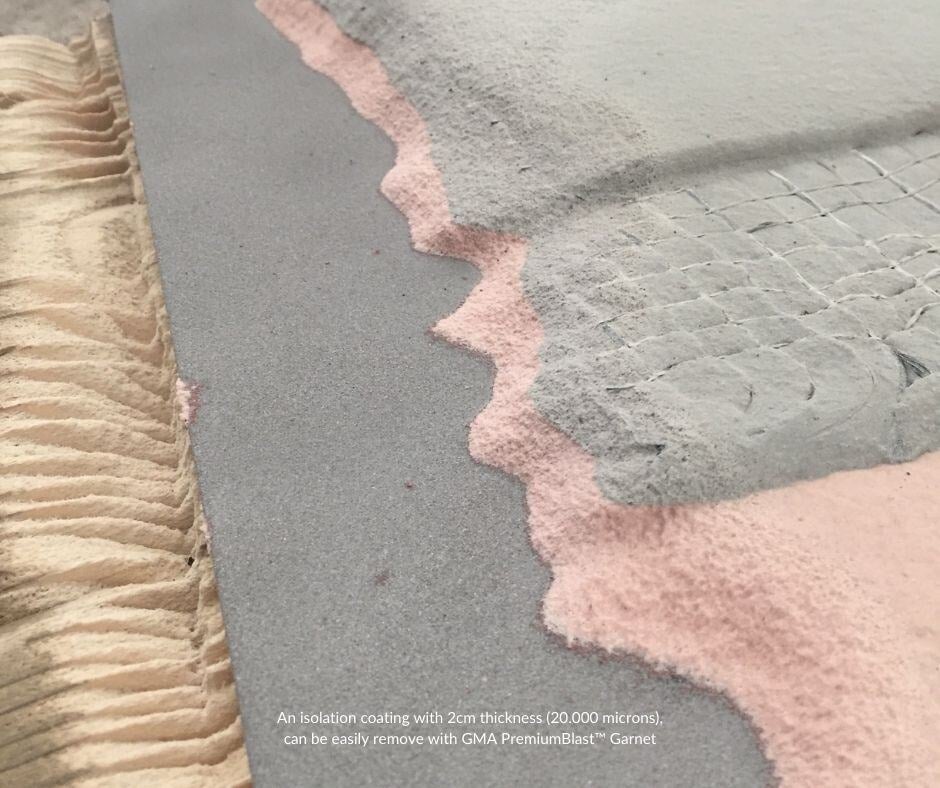
You’re currently viewing the Global website.

You’re currently viewing the Global website.
Would you like to switch countries or language?Blast Abrasives
Waterjet Cutting
Topics
Resources
Categories
Types
Categories
Topics
Abrasive Blasting Case Studies GMA PremiumBlast English Global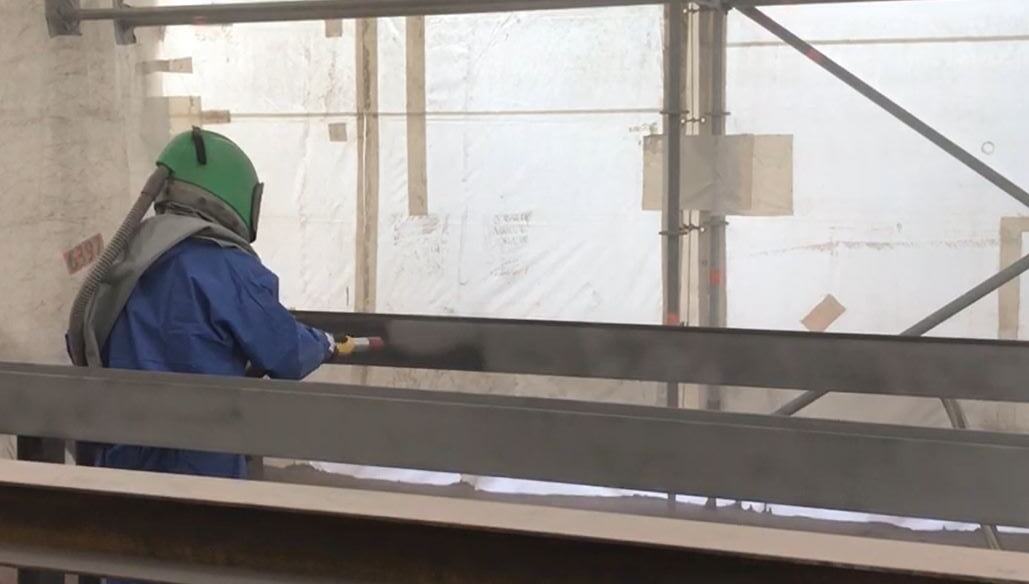
Cut consumption by 75% with GMA PremiumBlast™
Overview
Project
Improve working conditions across blasting sites
Location
Cologne, Germany
Task
Blast trial on site to test GMA PremiumBlast™ Garnet against coal slag
Challenge
To improve visibility and working conditions on site
Test Details
GMA PremiumBlast™ was tested on a test plate coated with 5mm lnterthem7050, 10 mm Chartek 7, and 50 μm of the base coating lnterplus 256.
ZÜBLIN Chimney and Refractory (ZCR) provides innovative solutions in refractory construction, chimney construction, structural fire protection, and technical insulation. The company’s services range from consulting and project planning through to service, maintenance, and documentation, as well as the reconstruction and refurbishment of industrial facilities.
ZCR had been using coal slag for their abrasive blasting projects across Europe. As the business grew, they were looking for ways to improve the working conditions for their workers, making it as clean and safe as possible. With coal slag, they experienced high levels of dust emission and impaired operator visibility, especially in enclosed areas. In addition, the abrasive consumption was high, and it took a long time to remove thick and heavy isolations coatings.
Total project consumption savings
A few months into using GMA PremiumBlast™, ZCR recorded a significant reduction in abrasive consumption of 75% for their ongoing projects. The current consumption rate is only 12.8kg/m² compared to abrasives which require 50kg/m². By switching to GMA PremiumBlast™, ZCR has achieved a cleaner and safer working environment for its workers while reducing abrasive consumption.
75%
less abrasive
Using GMA Premium BlastTM
Solution
To assess the current conditions and address these challenges, GMA teamed up with Elcometer, a blast and inspection equipment provider, and ZCR to conduct a blasting trial between GMA PremiumBlast™ and coal slag on site.
GMA PremiumBlast™
Trial Results
During the trial, there was a considerable reduction in dust levels, and operator visibility was greatly improved while blasting with GMA PremiumBlast™. The blasters’ blasting techniques were evaluated, and equipment settings were finetuned. By reducing the air pressure to 7 bar, which was less tiring for the blaster, GMA was able to optimize the abrasive flow while reducing abrasive consumption. Besides increasing the cleaning speed, especially for removing isolation coatings*, the blasted surfaces were free of embedment and other pollutants/contaminations.
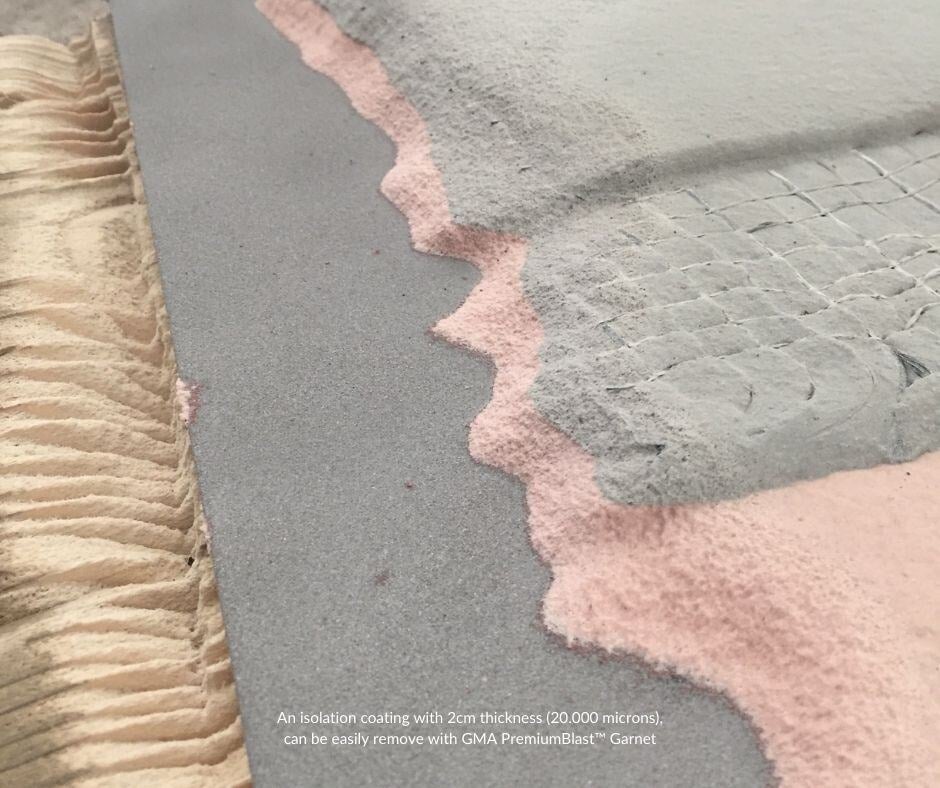
Key Project Outcomes
- Improved Working Conditions: The trial saw a significant reduction in dust levels, greatly improving operator visibility and creating a safer working environment.
- Optimized Abrasive Consumption: By fine-tuning the equipment settings and reducing air pressure, abrasive consumption was optimized, resulting in increased efficiency.
- Enhanced Surface Quality: The blasted surfaces were free of embedment and other pollutants, providing a cleaner result.
TruCost Abrasive Blasting Calculator
Summary
The transition to GMA PremiumBlast™ Garnet has not only improved the safety and working conditions for ZCR’s workers but also enhanced the efficiency and effectiveness of their blasting operations.
Read the full case study:
GMA PremiumBlast™ is not available in all markets however its low dust performance is consistent with the full GMA Garnet™ blast abrasives range. Speak to your regional expert about the GMA range in your market.
*GMA PremiumBlast™ was tested on a test plate coated with 5mm lnterthem 7050, 10 mm Chartek 7 and 50 µm of the base coating lnterplus 256.