You’re currently viewing the Americas website.

You’re currently viewing the Americas website.
Would you like to switch countries or language?Blast Abrasives
Topics
Waterjet Cutting
Topics
Resources
Categories
Types
Categories
Topics
Abrasive Blasting Case Studies GMA ToughBlast English Global Sustainability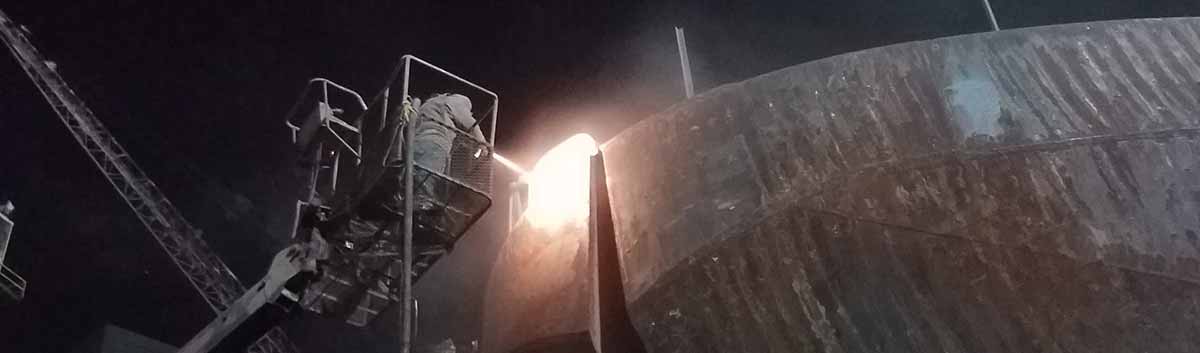
Low dust blasting increases efficiency for US Shipyard
Overview
Project
A shipyard in New York Harbor switched blasting abrasives to trial GMA ToughBlast™ garnet blast cleaning two steel ocean barges
Location
New York, U.S.
Surface Area
10,219m² (110,000ft²)
Task
Improve operational efficiency and reduce costs by addressing key issues associated with slag abrasives, including high dust levels and excessive abrasive consumption.
Challenge
High dust emissions, high consumption leading to frequent downtime for refilling, and costly disposal processes.
Challenge
Previously using slag abrasives, the shipyard had to contend with several key issues affecting their operational costs and productivity – dust, disposal of slag and scheduling abrasive delivery to keep up with production. Furthermore, the blasting operations were mainly conducted at night due to high dust levels. The shipyard used GMA ToughBlast™ garnet for blast cleaning two steel ocean barges with a surface area of 10,219m²(110,000ft²) to a commercial blast of SP-6 and achieved significant results.
Total consumption savings
Using GMA ToughBlast™ , the shipyard experienced substantial savings of up to 70% in abrasive consumption. The total garnet consumption was only 250 tonnes compared to 825 tonnes of copper slag typically required for a project of this size.
70%
Savings
Using GMA ToughBlastTM
Results
The reduced consumption rate resulted in less downtime required to refill the blasting pots. Rather than refilling the eight-tonne blasting pot every 2.5 hours when using slag, the change to GMA ToughBlast™ allowed workers to continue blasting throughout the night shift without interruption for refilling, which could then be completed by the day crew.
As a further convenience, refilling the blasting pot during the day could be completed by bulk bags rather than two 25t bulk tankers of slag per day. The use of bulk bags also meant that regular flat-bed trucks could make the deliveries while production continued and to stay on top of deliveries.
The result was an impressive increase in efficiency from each blaster covering 111m²(1200ft²) per night (using slag) to between 139 to 185m²(1500-2000ft²) per night using garnet. Furthermore, taking advantage of GMA’s used garnet returns program, each delivery vehicle was re-loaded with collected used garnet for return to GMA’s Fairless Hills processing plant. The easy management and removal of used abrasives reduced disposal costs to zero, completely eliminating the USD $150 per ton plus freight costs required to dispose of spent slag.
Low dust blasting with GMA Garnet™
Blast cleaning using GMA Garnet™ abrasives provides significantly lower dust emissions due to its inherent material toughness and rapid settling (high specific gravity). GMA Garnet™ is a naturally inert mineral, with its key characteristics of hardness, toughness, angularity, and density making it one of the most effective and efficient abrasives.
The lower dust emissions provide great improvements in operator visibility and safety on site while eliminating the constrain to only conduct blast cleaning at night due to the high dust levels created by slag abrasives.