-3.png?width=797&height=351&name=Table%202%20(797%20x%20437%20px)-3.png)
You’re currently viewing the Americas website.

You’re currently viewing the Americas website.
Would you like to switch countries or language?Blast Abrasives
Topics
Waterjet Cutting
Topics
Resources
Categories
Types
Categories
Topics
Abrasive Blasting Case Studies GMA ToughBlast English Global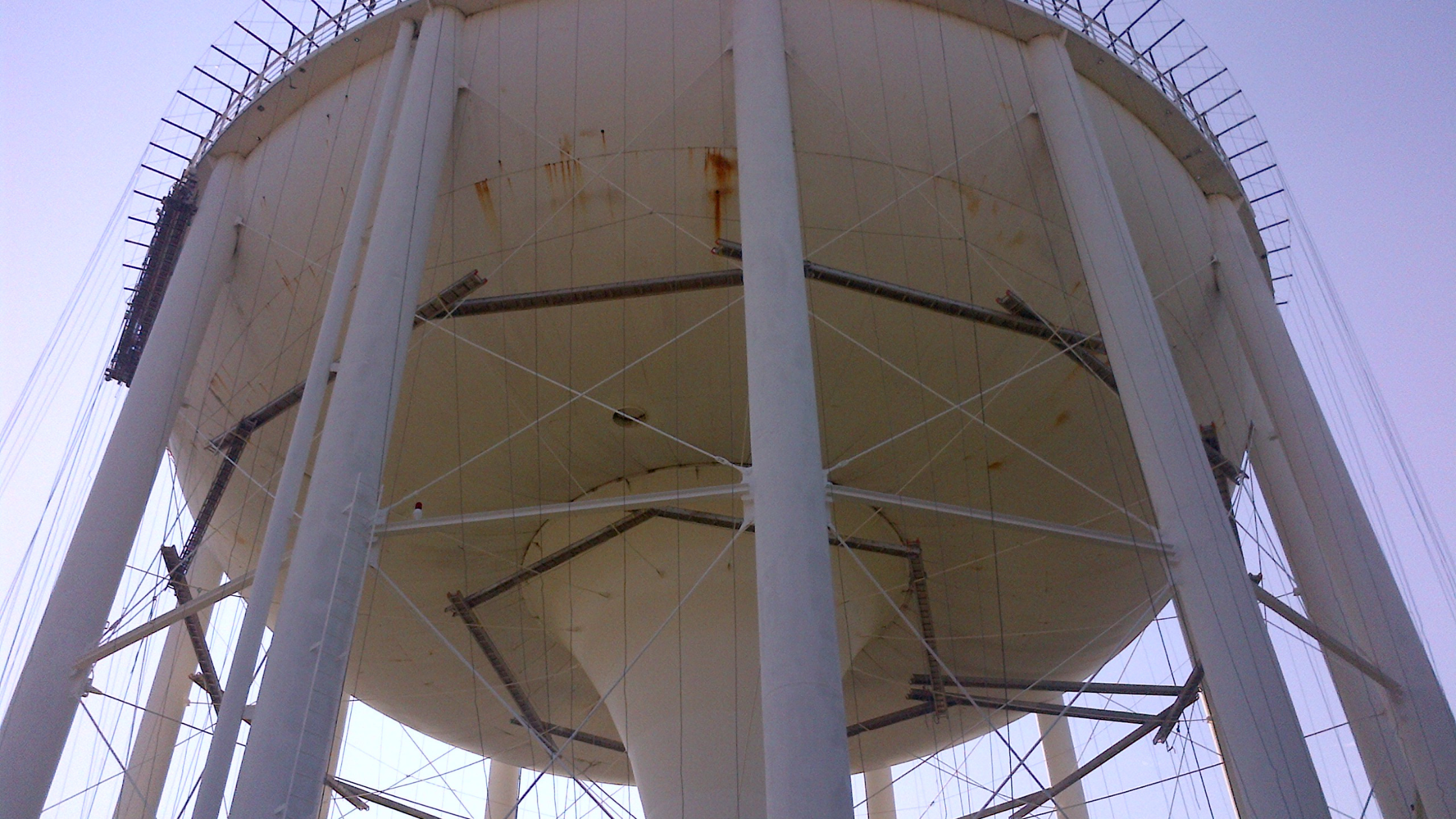
GMA ToughBlast™ saves 23 days in Water Tanks Maintenance Project
Overview
Project
Blasting of two water tanks
Location
Dayton, Ohio, USA
Task
Blast trial on two tanks during maintenance.
Challenge
Higher consumption, Lower productivity, achieved when using coal slag on Tank One.
A significant maintenance project involving two large multi-leg elevated water tanks, each with a capacity of two million gallons. The local painting contractor awarded the project used two different types of abrasive blasting products for each tank. Upon completion, the contractor found that one abrasive outperformed the other, resulting in a 22% total project cost saving.
Specifications
The tanks are supported by a central riser column and 12 peripheral legs. These structures are completely enclosed with tarps that can be adjusted for wind conditions. Access is provided via swing stages and catwalk platforms suspended between the columns. The tanks, which are 15 years old, have a total surface area of 6,782 m² (73,000 ft²) with a coating thickness of 25 to 30 mm. The internal surface area is 2,601 m² (28,000 ft²), while the external surface area is 4,181 m² (45,000 ft²).
Total project cost savings
7.7%
Savings
$26,576
Investment
Using GMA ToughBlastTM
Abrasive Blasting Process
Tank 1: Coal Slag Abrasive
The first tank was blasted using coal slag. The performance and cost-effectiveness of this abrasive were recorded for comparison.
Tank 2: GMA ToughBlast™ Garnet
The second tank, which had a thicker coating than the first, was blasted using GMA ToughBlast™ Garnet, recommended by BlastOne International, a GMA distributor partner. Two high-production MegaBlasters, each equipped with a 1,600-cfm compressor, were utilized for the task.
-3.png?width=797&height=351&name=Table%202%20(797%20x%20437%20px)-3.png)
“My working day is shorter as I don’t have to stop and wait for the dust to settle to see what we are doing. The visibility during the blasting session with GMA ToughBlast™ was excellent, significantly improving our efficiency.”
Project Foreman
Using GMA ToughBlast™
The foreman reported outstanding visibility during the blasting session with GMA ToughBlast™, a significant improvement over the coal slag used on the first tank. The enhanced visibility reduced downtime, as there was no need to wait for dust to settle, making the workday more efficient.

Productivity
37.7% or 72.5 ft²
Per hour more efficient

Consumption
42% or 160 tonnes
less abrasive

Labour
22.9 days or 60%
Less labour
Key Project Outcomes
- Overall time savings: 60% time saving, reduced from 43 days to 27 days.
Cost Savings: The use of GMA ToughBlast™ garnet resulted in a 7.7% reduction in total project costs. - Performance: The GMA ToughBlast™ provided superior performance, particularly noted in the blasting of the thicker coatings on the second tank.
- Efficiency: Improved visibility and reduced dust levels led to a shorter workday and higher overall productivity.
Summary
This case study highlights the advantages of using GMA ToughBlast™ garnet over traditional coal slag in large-scale maintenance projects. The superior performance, combined with significant cost savings and improved working conditions, demonstrates why GMA ToughBlast™ is a preferred choice for abrasive blasting in industrial maintenance.