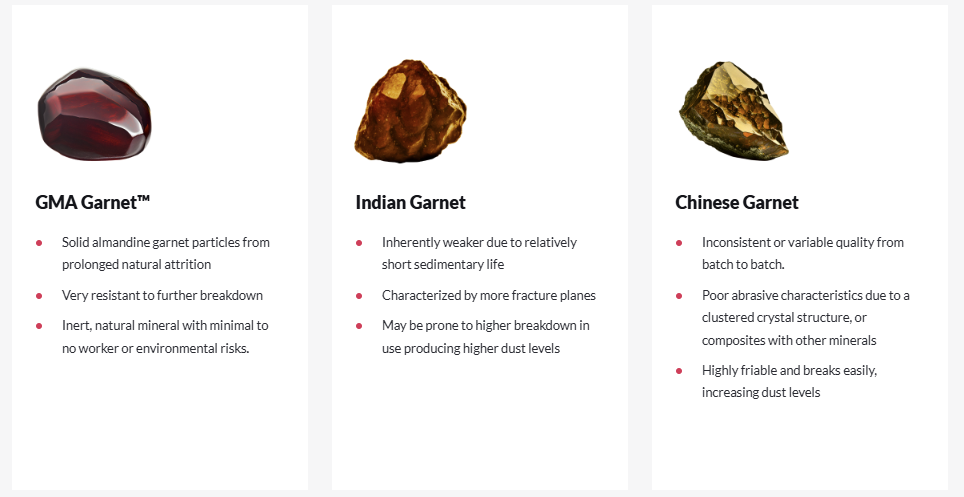
You’re currently viewing the Global website.

You’re currently viewing the Global website.
Would you like to switch countries or language?Blast Abrasives
Waterjet Cutting
Topics
Resources
Categories
Types
Categories
Topics
Abrasive Blasting Tech Tips English Global
Garnet vs. Slag – A Comparative Analysis
Choosing the right abrasive material is crucial for achieving the desired results in blasting operations. This blog delves into the comparison between garnet and slag abrasives.
Evolution of Garnet
Garnet has evolved over millions of years through the formation of igneous and metamorphic rocks under high pressures and temperatures. Older deposits, like those used by GMA Garnet™, contain a higher concentration of almandine garnet, which is a superior abrasive. The geological formation of garnet impacts its performance, making older deposits more effective due to their prolonged natural attrition, enhancing their abrasive properties.
Comparison of Garnet Types
GMA Garnet’s unique properties are derived from its geological formation. The high concentration of almandine garnet in older deposits results in higher hardness, toughness, and density compared to other types of garnet and slag abrasives. These properties make GMA Garnet™ a more effective and efficient abrasive material.
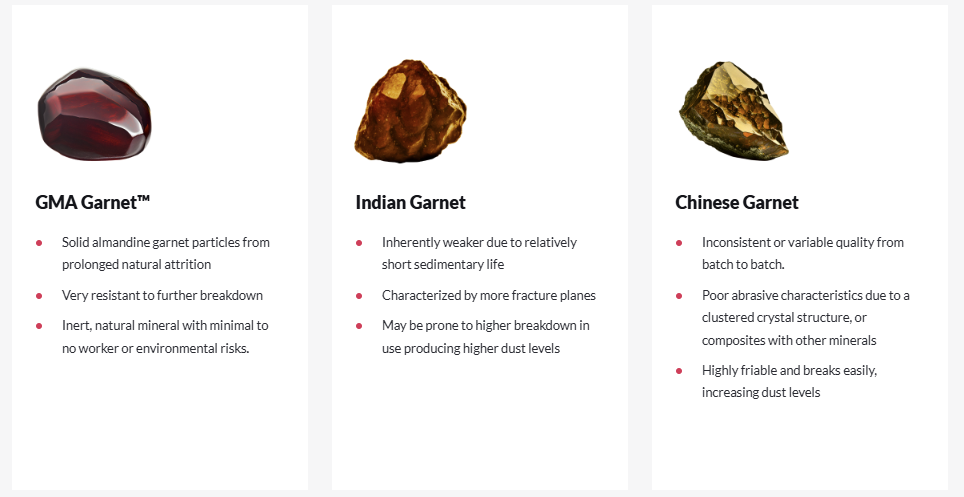
Slag vs. Garnet Abrasives
When comparing slag to garnet abrasives, GMA Garnet™ emerges as the optimal choice for several reasons:
- Lower Total Costs: GMA Garnet™ achieves lower total project costs compared to slag abrasives. This is due to a combination of factors including higher productivity, reduced consumption, and efficient waste management solutions.
- High Productivity: The hardness, toughness, density, and angularity of garnet, along with its ability to be used at higher pressures and in engineered blends, result in faster blasting times. Higher visibility in confined spaces also improves blasting operations, contributing to overall productivity.
- Reduced Consumption: Garnet's superior properties lead to more efficient usage, reducing the amount of material needed for the same blasting job compared to slag.
- Waste Clean-up/Management Solutions: Lower consumption of garnet means less waste to clean up and dispose of. Additionally, garnet can be reprocessed up to five times, supported by a return garnet program available in many global locations. This provides sustainable waste solutions and reduces overall environmental impact.
- Low Dust Blasting: The hardness, toughness, density, and angularity of garnet contribute to producing less dust. This, along with advanced processing techniques and turbidity control, reduces downtime waiting for dust to clear, improving overall efficiency and safety.
- Surface Quality: Garnet provides superior surface quality due to its engineered blends and peak density. GMA Garnet™ produces the cleanest surfaces with optimal surface profiles and minimal embedment. These qualities are supported by rigorous testing, including pull-off tests and other research.
- Worker Safety: Garnet's neutral and inert properties, combined with its low dust production and careful processing, minimize health risks to workers. This makes garnet a safer alternative compared to slag abrasives, which can contain hazardous heavy metals.
Sustainability
- Dangers of Environmental Contamination
Blasting with slag abrasives without containment poses serious risks to human health and threatens the environment. If not properly managed and contained, slags pose a high risk of contaminating soil and water bodies, including those that supply drinking water. - Recycling and Reuse
We encourage our customers to recycle and reuse GMA Garnet™. Through programs like the Returns Program in the US, we help you repurpose used garnet, ensuring it is effectively recycled and reused. Launched in November 2023, the Americas GMA Garnet Returns program allows GMA Americas customers to responsibly return used GMA Garnet™ for reprocessing and reuse, providing a cost-effective, sustainable solution to garnet disposal.