You’re currently viewing the Americas website.

You’re currently viewing the Americas website.
Would you like to switch countries or language?Blast Abrasives
Topics
Waterjet Cutting
Topics
Resources
Categories
Types
Categories
Topics
Abrasive Blasting Tech Tips English Global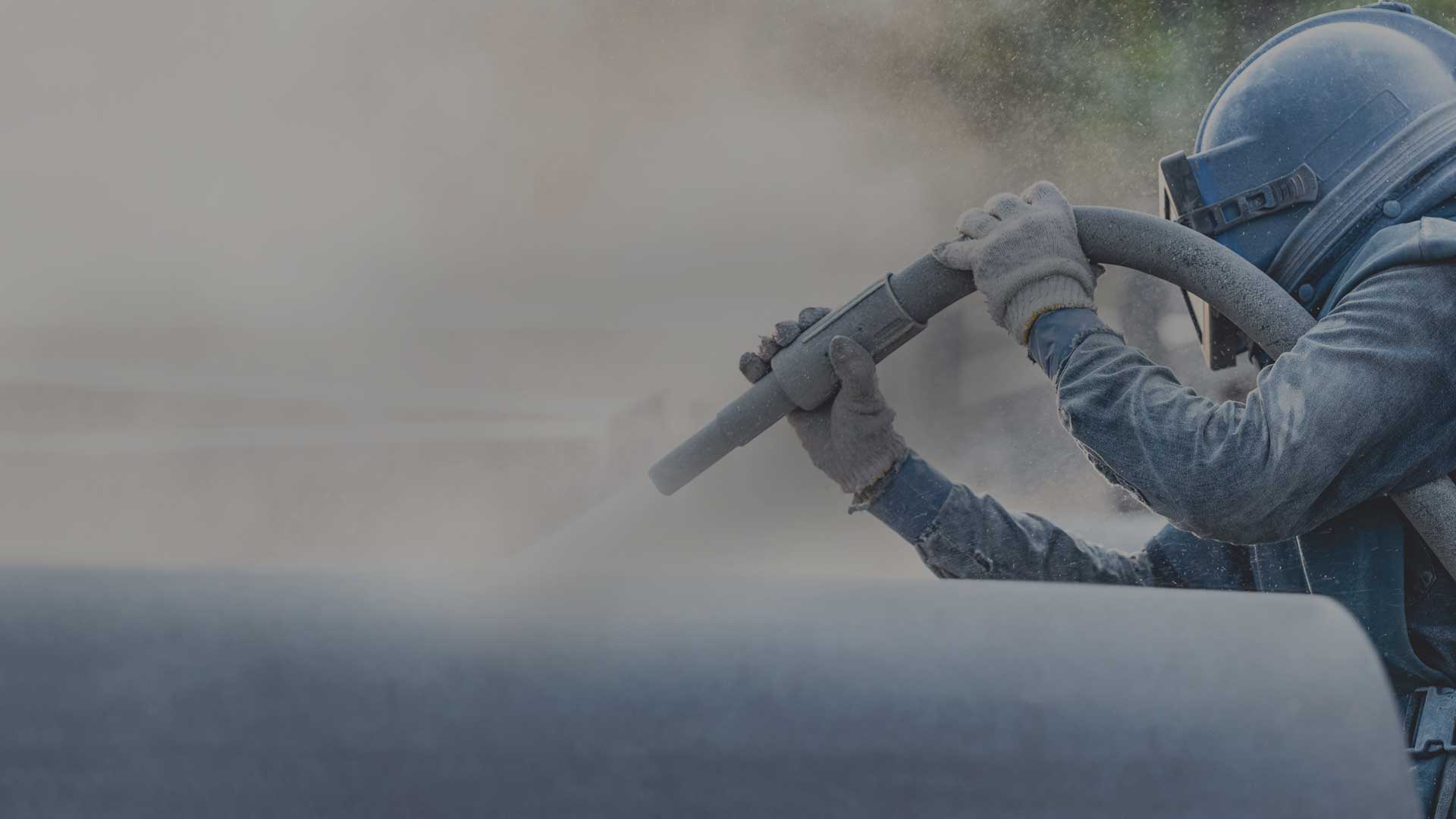
3 Simple Abrasive Blasting Procedures Saved a Contractor 34% on Costs
PrepCor*, a blasting and coating contractor in Adelaide, South Australia’s industrial heartland, successfully reduced project costs by a staggering 34% after making a few improvements including using GMA Garnet™ SpeedBlast™ abrasive.
In South Australia, where manufacturing and mining dominate the economy, there’s plenty of demand for abrasive blasting services. PrepCor’s business was flourishing, but underlining every successful project were sluggish inefficiencies that that could no longer be ignored. Like any good contractor, they wanted to discover what could be done.
Today, instead of pressing for immediate cost reductions, the team applies a more profitable, big-picture approach that includes GMA Garnet™ SpeedBlast™ abrasive media.
As you’ll see, investing in quality—upfront—is at the core of their overall savings.
Learning the Basic Truth: Cheaper Isn’t Always Better
PrepCor’s shift from focusing on cost, to capitalizing on value, didn’t mean simply switching to higher-quality abrasives. It started when they decided to take a logical approach to find the truth.
According to one industry consultant with over 45 years of blasting experience, “More often than not, contractors and project managers are “guesstimating” or going off of their gut feelings when making decisions.”
Take PrepCor’s original approach, for example.
They were cutting every cost possible with the reasonable, but flawed, intention to save money. Rather than focusing on performance, they always used the lowest-priced abrasives. Instead of saving, this decision ended up costing more due to losses in blasting productivity and efficiency.
When it comes to blasting projects, skimping on quality creates inefficiencies throughout the entire project. And they add up.
Scheduling a Full Blasting Assessment
First, PrepCor found a supplier of quality abrasive media; GMA has been supplying the industry for over 35 years. However, investing in quality only pays off if you know how to use it.
Then, PrepCor engaged specialists to help them figure out where they were going wrong—a world-class abrasive supplier, GMA, and a leading industry consultant, BlastOne International. As strategic partners, these two companies had plenty of experience unlocking the potential of blasting contractors.
Together, the team ran an extensive assessment of PrepCor’s blast cleaning and painting process, measuring everything from compressor and nozzle air pressures to abrasive consumption.
The experts recommended three simple changes:
1) Use high-performance GMA Garnet™ SpeedBlast™ garnet abrasive.
Garnet is a quality abrasive media with a higher initial purchase cost than some materials, such as slag. But if you let the price scare you, you’re selling yourself short by not calculating its future potential, as garnet outpaces lesser abrasives due to its hardness, low consumption rates, and durability. With the wrong abrasive, you’ll end up spending more in the long run.
2) Remove a series of inefficient air driers and install a moisture removal system.
It’s common knowledge that when blasting abrasive gets moist, it clumps. But how does that affect costs? With even small amounts of moisture (such as humidity) in the blasting pot, completely opening the valve may be the only way to get flow to the blastline. This technique wastes abrasive, and your profits (literally) blow away.
3) Add micro-valves for accurate metering of the garnet.
For some blasting operators, getting work done faster means cranking up the flow of abrasive. But you’ll reach a point where using more isn’t better—it’s wasteful and costly. Defend profitability by dialing in the metering valve to the proper flow.
In addition to the above recommendations, the technical experts of GMA and BlastOne uncovered a game-changer during the blast assessment.
The combination of dry air and higher quality GMA Garnet™ SpeedBlast™ garnet meant the blasting team could close the abrasive metering valves by half a turn without sacrificing productivity.
This increased blasting speed by 25%, and reduced abrasive consumption by nearly 50%!
More benefits of honing the blast pressure, removing the moisture, and using GMA Garnet™ SpeedBlast™:
- Uninterrupted blasting for nearly two hours without having to refill the blast, previously filled every 45 minutes.
- Only two out of three compressors were required to complete the job due to a gain in pressure (13psi).
- Costs were reduced by 10% by capturing lost energy, saving $1,200 AUD per month.
- Low-dusting GMA Garnet™ SpeedBlast™ cut abrasive consumption and prolonged the life span of the dust collector filters, blast hoses, and the nozzle.
Two tips for those looking to achieve these results
All blasting companies are looking to make their projects more profitable. If you’re investing in quality to maximize value, here’s some advice based on 35 years of blasting experience.
Measure everything, don’t assume.
Ask most blast operators how a job went, and you’ll get something along the lines of, “It was tough, but we got more done than yesterday.” This isn’t good enough. To improve operations, you need data and specific metrics, not vague estimates.
Engage an experienced abrasive media consultant.
Using new equipment and abrasive media doesn’t guarantee profits. Results come faster with the guidance of a skilled blasting abrasive consultant on your side. Anything less is a waste of time and money.
Let's talk about your abrasive blasting procedure challenges and how GMA Garnet™ changes the game.
*Blasting contractor’s business name altered for confidentiality.