You’re currently viewing the Americas website.

You’re currently viewing the Americas website.
Would you like to switch countries or language?Blast Abrasives
Topics
Waterjet Cutting
Topics
Resources
Categories
Types
Categories
Topics
Waterjet Cutting Tech Tips English GlobalWaterjet Cutting abrasives: There’s no one size fits all
Versatility is one of the main attractions to waterjet cutting and why they have become so popular in the manufacturing industry. Much like manufacturing operations, there is no “one size fits all” anymore, as situations change from one day to the next.
From cutting ferrous to non-ferrous metals such as carbon steel, stainless steel, aluminum, alloy, high nickel materials and even AR (abrasion resistant) plate. Waterjet machines are also very common in stone and tile shops, and glass cutting as well. They can offer a high precision cut, for both edge quality and any ornate or intricate cutouts.
Of course, with any waterjet cutting operation that requires abrasive, the garnet you use can have a significant impact. That is where GMA separates itself from the competition, and why GMA Garnet™ is the predominant choice for waterjet machines in the U.S. and around the world.
For many years, 80 mesh alluvial garnet, such as our ClassicCut™ 80 has been the industry standard for most applications. And to this day, it has stood the test of time and is the clear choice for more waterjet machines in the U.S. than any other garnet. But when it comes to cutting other materials, in some cases, there can be better options.
For example, some of our stainless steel service centers that process several thousand tons of stainless plate a year; many have chosen to use our Procut™ 60. It is coarser and is one of our engineered blends that we developed after many hours of Research & Development that included different blending ratios and real world cutting, (both in-house and at customers facilities). When test cutting 1.5” thick 304 SS plates, the average cutting speed is 20% faster than the regular 60 mesh alluvial garnet, all while achieving the same edge quality.
Time is money, and if we can help our customers increase their performance, they become more profitable in the process. It can be used for both - a finish cut, or in some cases where speed is more important, it can also be used for a rough cut as a first operation. Unlike plasma or oxy fuel, you won’t have any heat affected zones. And when cutting medium or higher carbon steel such as 1045, you won’t have to stress relieve or anneal after a waterjet cut; as you do after flame cutting.
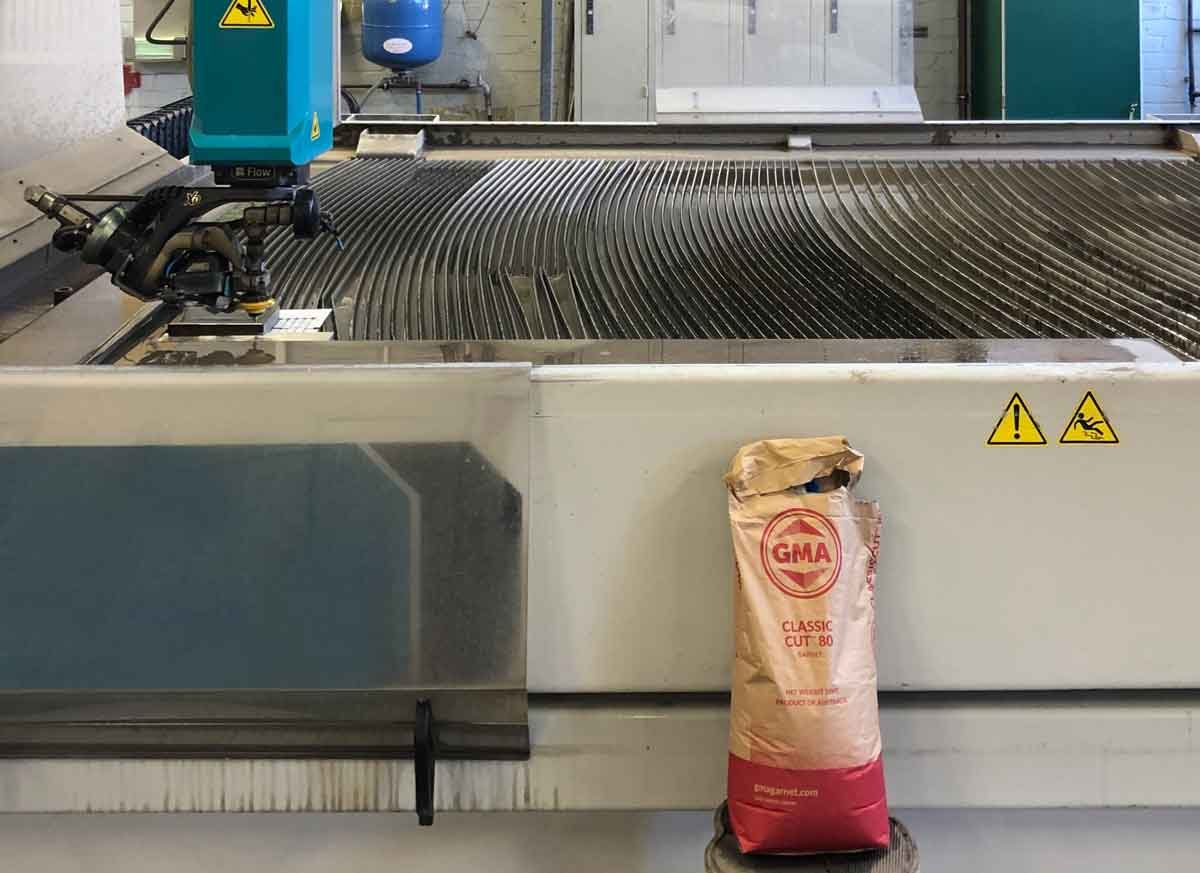
Either instance can ruin the part you are cutting. That’s why it’s so important to use a quality, consistent abrasive every time to avoid any issues.
Did you know that every bag of GMA Garnet™ sold in the U.S. has been processed, screened and packaged before it leaves our facilities? Along with constant QC checks in place, it’s not hard to see why GMA Garnet™ is the most popular garnet for waterjet machines in the U.S. and around the world.
These are just a couple of examples where dealing with the right garnet company can make a big difference in your waterjet cutting operations. From increasing performance and cut quality, which in turn increases profitability. This is also where our GMA team of experts can really help you.
If you haven’t, reach out to your GMA sales representative to ensure you are using the right abrasive for your application. Contact us today: info.us@gmagarnet.com