You’re currently viewing the Americas website.

You’re currently viewing the Americas website.
Would you like to switch countries or language?Blast Abrasives
Topics
Waterjet Cutting
Topics
Resources
Categories
Types
Categories
Topics
Abrasive Blasting Tech Tips English Global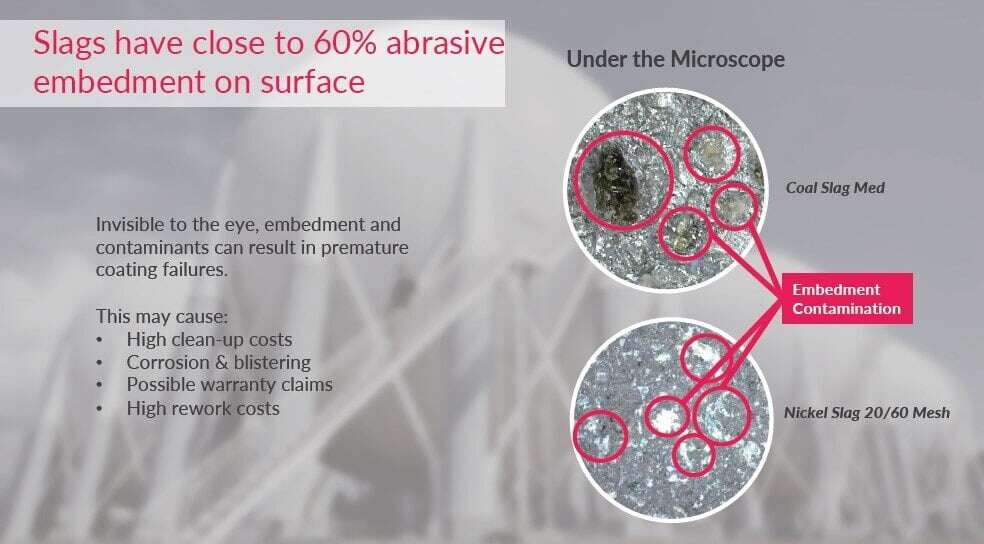
The Hidden Impact of Abrasive Embedment on Blasted Surfaces: Ensuring Clean White Metal
Corrosion engineers and coating specifiers, understand that proper surface preparation is the cornerstone of successful projects. This BlastTalk will discuss an often-overlooked aspect of abrasive blasting – abrasive embedment – and how it can lead to surface contamination, jeopardizing project integrity and potentially reducing coating life.
In the pursuit of achieving superior corrosion control and coating performance, surface preparation plays a critical role. Neglecting this stage can result in up to 80 to 85% of coating failures, underscoring the need for meticulous attention to detail.
Blasting classifications such as SP5 (white metal) and SP10 (NACE2 near white) are well-known standards within the industry. However, the focus often lies primarily on coating specifications, with minimal emphasis on the nuances of surface preparation.
Through extensive research and magnification studies, the impact of abrasive embedment on blasted surfaces becomes evident. Embedment occurs when abrasive particles stick or become embedded into the metal surface during blasting. While some abrasives leave minimal traces, others deposit contaminants, leading to potential coating adhesion issues.
Observing various abrasive products on the market, two distinct behaviors emerge. First, there are angular and friable crystals that tend to shatter and embed into the surface. Second, some abrasives appear as though they splatter onto the steel, akin to paintball marks, forming a clay-like film on the metal.
By-products such as slags can feature angular fragments that create heavy embedment. On the other hand, certain natural minerals, even those considered ideal for white metal surfaces, may contain softer minerals that result in surface caking.
Contamination from abrasive materials, whether by-products like slags and glass or natural minerals, poses a significant risk to coating adhesion. These impurities can cake onto the surface, misleading the naked eye and leading to the false assumption of a clean white metal surface.
Backscatter microscopy offers deeper insights into surface quality. It can identify embedded particles and contaminants that may otherwise remain unnoticed, enabling a more accurate assessment of surface cleanliness. Slags can embed particles up to 60-70% of the overall surface area and a lot of times give false profile readings.
To comprehend the variance in coating adhesion strength, 3D peak density tests are employed. Abrasives with higher peak densities generally yield stronger adhesion, whereas those with lower densities may result in weaker bonding.
Merely adhering to SP5 or SP10 standards may not guarantee a genuinely clean white metal surface. For facility owners, coating manufacturers, and stakeholders invested in a project's outcome, specifying abrasives that leave true white metal surfaces becomes imperative.
In conclusion, the impact of abrasive embedment on blasted surfaces is a crucial factor in ensuring coating longevity and integrity. By delving deeper into the realm of surface preparation and selecting abrasives that minimize contamination, corrosion engineers and coating specifiers can elevate project outcomes and optimize coating performance.
As professionals entrusted with safeguarding the longevity of assets, let us embrace the critical role of meticulous surface preparation and the importance of accurate abrasive selection. By prioritizing the quest for true clean white metal surfaces, we can bolster project success and ensure the enduring performance of vital structures.
Written by Pete Mitchell
VP New Market Development and
Technical Management