You’re currently viewing the Americas website.

You’re currently viewing the Americas website.
Would you like to switch countries or language?Blast Abrasives
Topics
Waterjet Cutting
Topics
Resources
Categories
Types
Categories
Topics
Abrasive Blasting Our Customers English Australia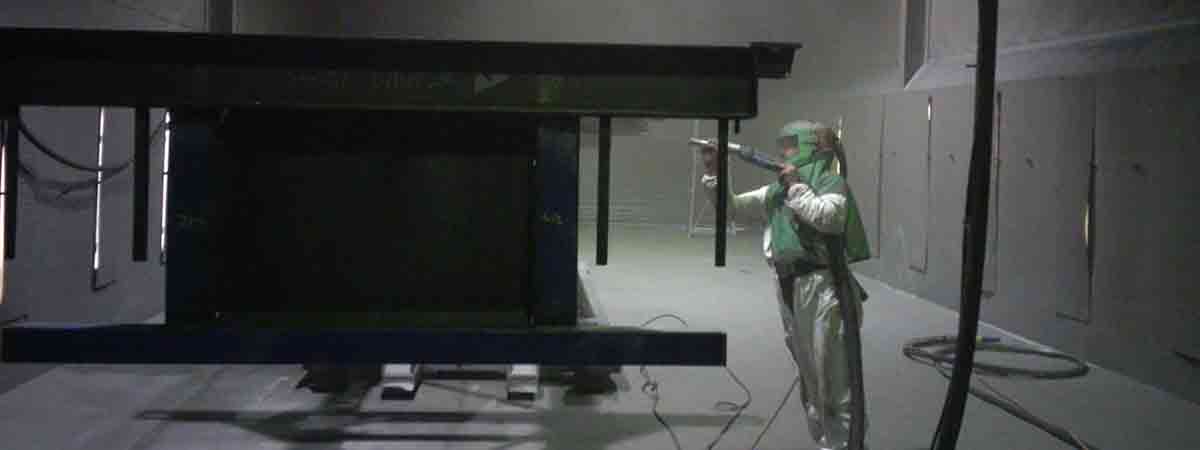
Steel grit user doubles production by switching to GMA Speedblast
A manufacturer in Brisbane, Australia has been building rubbish truck bodies from mild steel for several years.
The blasting and painting of the fabricated truck bodies were performed in their old blast room that is equipped with an auger system. According to the blaster, they used steel grit abrasive to prepare the surface, and they may spend seven to eight hours of blasting time on one truck body.
Besides the long hours, the painters were unhappy with the quality of the blasting as a significant amount of grit residue was found on the surface, which greatly affected the paint finish.
Furthermore, they experienced downtime when the auger came in contact with water. It took a day to dry and clean up the rust caused by the grit. Moreover, the blast helmet lens and overalls were frequently replaced due to ricochet of the steel grit off the surface.
In fact, the steel grit dust that landed on the roof also damaged the solar panels.
Seeing the need for a solution to these problems, the company contacted BlastOne - a long-term distribution partner of GMA.
BlastOne recommended that they switch to GMA SpeedBlast garnet abrasive, and the results were beyond their expectations:
- The blasting time was reduced by half from eight to four hours per truck, and they doubled the production by completing two truck bodies a day.
- Significant improvements in blasting quality and surface cleanliness were realised.
- Ease of cleaning after blasting was noted, especially during the blow off process. The distinct colour of GMA SpeedBlast enables them to clean the surface more thoroughly in comparison to steel grit, which has a similar colour to the steel surface.
- Visibility is improved during blasting due to the low dust characteristics of garnet.
- Downtime to dry and clean up the blast room is greatly reduced to just a few minutes, instead of an entire day, as garnet will not rust up the auger.
The company is pleased with the significant improvements to productivity and product quality, resulting in less disruption to their project schedule due to minimal downtime.