You’re currently viewing the Americas website.

You’re currently viewing the Americas website.
Would you like to switch countries or language?Blast Abrasives
Topics
Waterjet Cutting
Topics
Resources
Categories
Types
Categories
Topics
Waterjet Cutting Our Customers English Global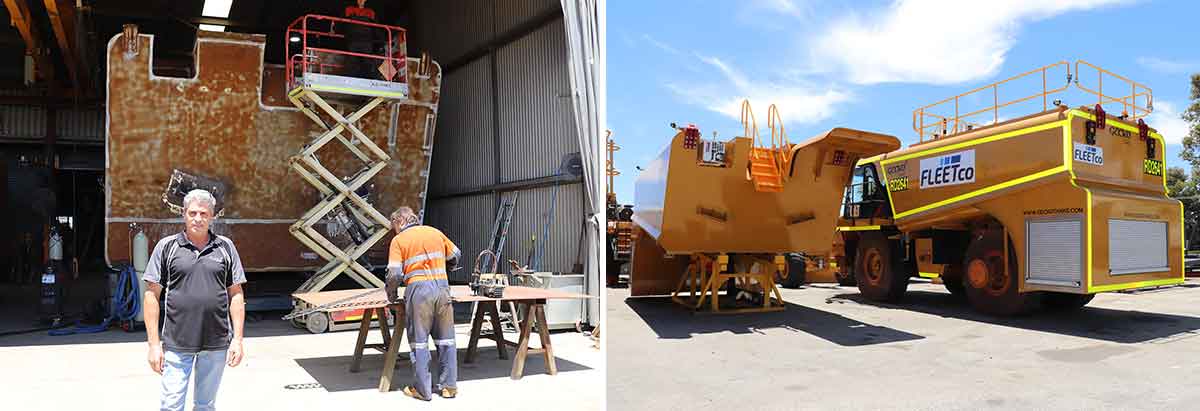
Steady supply of abrasives helps Manuel manages deadlines
GMA PremiumBlast™ is cleaner and safer.
Every day, Blast & Paint Manager Manuel Villar from Alpha Plant runs a tight schedule dealing with customers, working on estimates and overseeing the projects from the beginning to the end.
Alpha Plant specializes in sales, hire, repairs, import and export of heavy equipment in Australia, Asia and the Americas.
The company also provides blasting and painting, and fabrication services. With over 30 years of experience in the Blast and Paint industry, automotive painting and panel repairs as well as industrial metal blasting and spray painting, Manuel works with major customers from mining, civil, agricultural, protective coatings and oil & gas.
Managing various projects with different specifications and requirements including resource allocation can be challenging, but according to Manuel, one of his key challenges is meeting deadlines.
“Customers want everything yesterday. They are investing over a million dollars on the equipment, and they would want it to be ready without any delays,” Manuel explained.
However, some delays are beyond his control. He may be the last in line to work on the project which is already behind schedule, or he needs additional days or weeks to fix a technical issue on the equipment. Moreover, the blasting and painting process can be weather dependant, and you also need to wait for the paint to cure. Manuel addresses these challenges by managing his project schedules well to catch up on lost time.
Over the last 20 years, Manuel has used many types of blasting media, and his preference is GMA PremiumBlast™ garnet.
“Simple reason. It’s cleaner, safer, less dust with no issues,” Manuel said.
“I’ve used other garnet abrasives in the past, and the supply was not constant. I don’t know when I will get my next order, and I had to buy large quantities like 40 tonnes at a time.”
Manuel added that with GMA PremiumBlast™, he could blast quicker. As there’s no contamination in the product, he is confident that he can pass the required quality and specification requirements, namely chlorine and adhesion tests.
He also shared that if you use the right abrasives, test your blast pressure, and check for equipment wear and tear before every blast, you can do it 10 times quicker. For him, the optimum blasting pressure is between 90-105 psi with full production at 105psi.
Manuel’s company also manufactures the Gecko tank, a custom-designed off-highway water carts and fuel / lube trucks. For more information, visit alphaplant.com.au