You’re currently viewing the Americas website.

You’re currently viewing the Americas website.
Would you like to switch countries or language?Blast Abrasives
Topics
Waterjet Cutting
Topics
Resources
Categories
Types
Categories
Topics
Waterjet Cutting Tech Tips English Global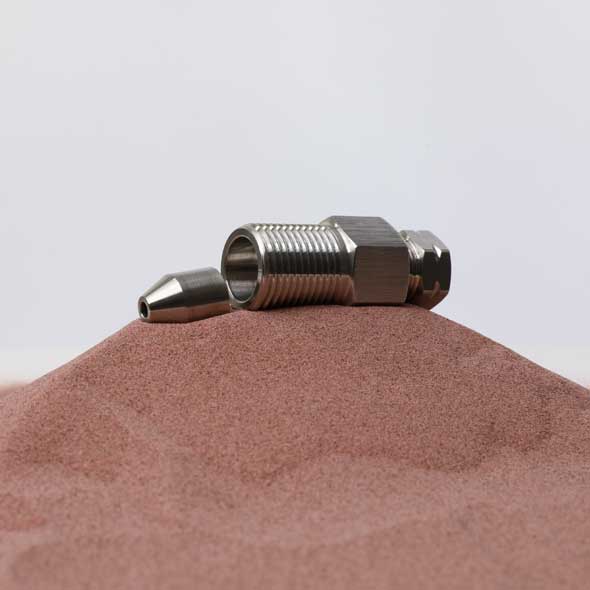
Selecting the Right Equipment to Optimize Your Waterjet Cutting Process
How to Maximize Waterjet Cutting Speed and Minimize Costs
What Equipment Is Ideal for Abrasive Jet Cutting?
As you know, when garnet abrasives are added to the waterjet stream, the abrasive particles travel at three times the speed of sound. You can increase the waterjet cutting speed by adding more abrasives to the waterjet stream. However, adding too much abrasive will rob speed and energy from the waterjet stream and the cutting speed will start to decrease. That’s why waterjet manufacturers conduct extensive testing with various orifice and nozzle combinations to find the optimum abrasive amount with consideration of waterjet cutting speed and cost.
Selecting Your Waterjet Orifice
When it comes to waterjet orifice selection, we can just refer to an orifice selection chart supplied by the pump manufacturer as their design engineers have done most of the calculations for us. From this chart, you can easily pick a 0.014” orifice or two 0.010” orifices for the 50 HP pump.
Choosing Your Nozzle (Focusing Tube)
As a general rule, the orifice diameter should be approximately three times the size of the water nozzle orifice. While some users would recommend a smaller ratio of about 2.5 times to produce faster waterjet cutting speeds, there are trade-offs. It could cause an increase in nozzle wear and part tolerance which translate to more costs. Moreover, the wrong combination can also affect the cutting quality. Many waterjet cutting users tend to operate with the standard combinations that are commonly practiced or promoted in the industry. It may be worth exploring different combinations that could help reduce your orifice and nozzle wear and tear while obtaining a better cutting quality for your project.
Below are the possible combinations*:
Selecting Your Garnet Abrasive
Garnet has been used for decades as an abrasive in waterjet cutting due to its superior physical properties. When added to high pressure streams of water, garnet abrasive is capable of cutting through tough materials including steel, aluminum, stone and Inconel. Currently, the use of abrasive jet cutting in the natural stone industry is increasing. Its effectiveness on natural stones depends on the properties of the stone and machine operating parameters. Stone (marble, ceramic and granite) is softer material compared to metal. Using finer garnet particle sizes can help achieve a smoother surface finish on softer materials. Industry standards denote that garnet sizes ranging from 80 mesh to 120 mesh deliver the optimum performance in most applications in industrial abrasive jet cutting operations. GMA Garnet™ is well known in the industry as a pure and accurately sized garnet abrasive with no dust or ineffective grains to restrict garnet free flow.
*Note: User discretion is advised when following these recommendations. GMA is not responsible for any performance damages resulting from the use of information presented in this chart.
Ready to Optimize Your Waterjet Cutting Process?
Investing in high quality nozzle, orifice and effective garnet abrasives such as GMA Garnet™ for your waterjet cutting machine will enhance the performance and precision of your cutting applications.
You can take this further by setting up the ideal combination of the size of garnet abrasives along with nozzle and orifice to get the best precision cutting.
Contact us to learn more about how you can maximize cutting speed without increasing costs with GMA Garnet™.