You’re currently viewing the Americas website.

You’re currently viewing the Americas website.
Would you like to switch countries or language?Blast Abrasives
Topics
Waterjet Cutting
Topics
Resources
Categories
Types
Categories
Topics
Abrasive Blasting Tech Tips English Global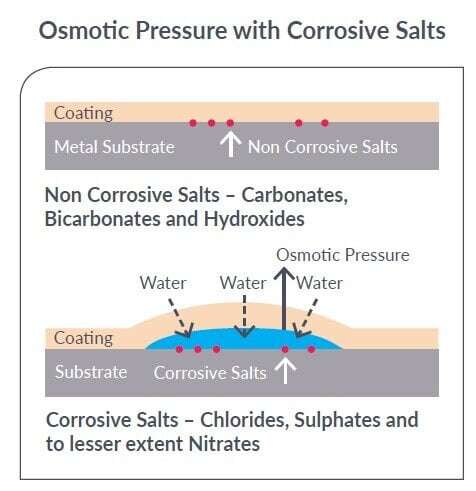
Salts ain’t Salts
When it comes to measuring salts and their potential impact on corrosion not all salts are the same.
There are numerous methods of measuring surface salts as well as numerous variables that can lead to optimal coating performance. But there is data that proves there is a direct correlation between the presence of soluble salts and premature coating failure 1-4.
Blasting abrasives are a key factor in moving salts but there are numerous sources
of garnet abrasives around the world each with their own unique geological characteristics. This actually applies to all abrasives as well.
Garnets such as many Indian/Chinese river garnets are younger and have minimally formed carbonate minerals. These garnets are usually more friable, with higher fractures and are lower quality.
Not all salts are corrosive
Not all salts are corrosive salts and many salt contaminants will not induce corrosion. It is important to understand which salts are corrosive and which will not induce corrosion.
The non-corrosive or non-harmful soluble salts on metals are:
- Carbonates
- Bicarbonates
- Hydroxides
Coating films are semi-permeable membranes and when there are salt contaminants of chlorides and sulphates under the coating surface there is a tendency for water diffusing into the coatings to equilibrate the concentration.
This causes delamination and blistering. Osmotic blistering is one of the most common coating failures. Carbonates and Bicarbonates do not cause delamination and osmotic blistering.
The most harmful corrosive soluble salts on metals are:
- Chlorides
- Sulphates
- Nitrates
Methods of Assessment
Standards such as ISO 8502 presents methods of assessing salts and provide guidance to many specifiers, coating, and corrosion specialists as well as asset owners and contractors in many countries around the globe.
There has been numerous reports and investigations concluding that methods of testing and analysis of corrosive salts needs to be revised and updated. While the methods described in ISO 8502-9 can be used to determine the presence of water-soluble salts, this does not accurately indicate the presence of corrosive salts.
There is a solution!
Discuss with the Project Specification Manager or Consultant to include the following addendums to the project specification:
- Specify an ion specific test kit that measures Chlorides, Sulphates and Nitrates based on agreed testing and analysis methods
- If using the current ISO 8502-9 method and the resulting calculation shows a Total Surface Density level above the specified limit, a secondary ion specific test is required to determine if corrosive salts are present above the limit.
Alternatively, contact your GMA Sales Representative for expert advice on specification adjustment and testing procedures.
1 D.G. Weldon, T.A. Caine, Proc. of SSPC Symposium, held May 1985 (Pittsburgh, PA: SSPC, 1985). 2 G.C. Soltz, “The Effects of Substrate Contaminants on the Life of Epoxy Coatings Submerged in Sea Water,” NSRP Report, TASK No. 3-84-2, March 1991. 3 M. Morcillo, J. Simancas, JPCL 14, 9 (1997): p. 40. 4 H. Mitschke, “Effects of Chloride Contamination on the Performance of Tank and Vessel Linings,” JPCL 18, 3 (2001): p. 49.