You’re currently viewing the Americas website.

You’re currently viewing the Americas website.
Would you like to switch countries or language?Blast Abrasives
Topics
Waterjet Cutting
Topics
Resources
Categories
Types
Categories
Topics
Waterjet Cutting Tech Tips English Global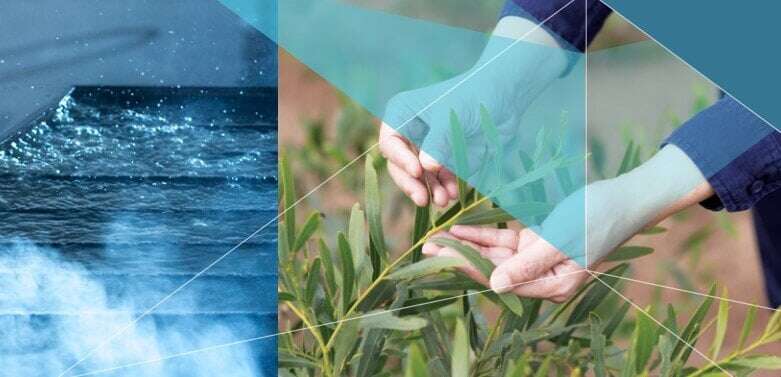
Garnet reprocessing and waste handling solutions
Environmental sustainability has become a concept in many parts of the world and a topic that will certainly develop in the future, and as a supplier we also have a responsibility and an obligation to contribute.
The waterjet cutting process checks all the right boxes when it comes to sustainability. Environmentally beneficial advantages include no slag formation or dross waste, and no creation of any toxic fumes or greenhouse gases.
The main cutting medium of water is recyclable and there is no need for any post processing tasks such as heat treatments, reducing the impact on the environment. In addition, no cooling oils or lubricants are required as the water jet itself acts as a coolant.
Abrasive Waterjet Cutting is essentially an accelerated erosion process. Ultrahigh-pressure water is fired through a ruby or tetraCORE diamond orifice into a mixing chamber, which creates a vacuum and draws garnet sand into the water stream. In connection with the cutting, residual products such as garnet cutting abrasive and various metals in particle form are also produced, depending on which metal is being cut.
Is Used Abrasive Hazardous Waste?
Garnet, the typical waterjet abrasive, is an inert, naturally occurring, semiprecious mineral. It is either natural garnet grains from our mine in Western Australia (alluvial garnet) and are very resistant to further breakdown compared to any other garnet from China or India or mined out of the mountains in Montana (crushed rock garnet).
So, is used abrasive hazardous waste?
It depends on what you're cutting and how much. If you are cutting lead or beryllium copper, then you may have a hazardous waste situation. For most other materials, the amount of the scrap material in the abrasive is so small that it is rarely a problem. Even most stainless steels are usually not an issue unless they contain a high nickel or chrome content.
With waterjet cutting, you are pulverizing the cut material and not structurally changing the material like with electrical discharge machining. Therefore, most of the impurities in waterjet overflow water are suspended solids, not dissolved.
The Cost-Effective Option for Used Waterjet and Abrasive Blast Media Disposal?
It is expensive in terms of logistics, packaging, and labor to find ways to dispose of used garnet. Due to GMA Garnet’s superior toughness and low friability, GMA Garnet™ abrasive can be recycled up to five times without compromising its reliable, high-quality performance.
At our garnet reprocessing facilities, we first clean spent garnet sourced from blasting and waterjet cutting activities to remove all contaminants, including dust, rust, paint flakes and metallic particles. Then we precisely size the garnet into various grades to suit customer requirements. Strict sampling and quality control procedures ensure that sizing and purity are maintained to our own industry best standards.
As our customers become increasingly focused on economic and environmentally responsible disposal solutions to manage their spent garnet, GMA stands ready with complete life cycle solutions.
To achieve the best result after the incoming waste running through the reprocessing plant, it is of great importance which material we receive from our customers, and it is therefore important that there is a good balance between the particle sizes to produce garnet for micro and waterjet cutting.
Incoming waste from our Waterjet customers depending on the material that has been cut, pressure and thickness of the material, such as: stone, glass, stainless steel, and hardox, or whether 4000 or 6000 bar pressure has been used for cutting.
Garnet reprocessing system requires a significant capital investment, which means that the establishment of such reprocessing plants requires access to large quantities of waste, within a reasonable distance, as transport constitutes a large part of the total costs.
How does the GMA Garnet™ waste management program work?
GMA's waste management program is currently operating in Italy, Dubai and America. Before returning used garnet, it is reviewed by GMA on a case by case basis, with the customer then ensuring it is environmentally safe to transport and process.
To ensure all loads of garnet are nonhazardous and an analysis must be prepared at an accredited laboratory. Next, GMA need a sample for sizing analysis to see whether we can get value from reprocessing the garnet or not.
Are there other sustainable options to offer customers in our reprocessing plants?
It is of great importance that, as a responsible supplier, you can offer other options that cater to customers where reprocessing is not possible, because of unreasonably high transport prices or areas/countries where reprocessing is not possible or profitable because of too low volume.
Waste disposal, landfill or reprocessed as a raw material?
In many countries in Europe and USA, waste from Waterjet is handled differently by the authorities and right down to the municipality/county level. We experience that the product is analyzed in different ways across different countries and overall it reveals we are at times quite a few steps away from looking into alternative ways to include waste from Waterjet as a raw product, for example, asphalt or concrete industry. The majority of all analyzes comply with applicable limit values and a large part of this is used as landfill.
At the same time, we see major problems in transporting waste across national borders, even if the purpose of this is to make use of our reprocessing facilities.
Fortunately, over many years throughout the world, we have built up competence in this area, which enables us to reprocess and offer alternative sustainable solutions.
Finally, it is the responsibility of the waste generator to ensure that spent materials are disposed in accordance with applicable solid waste regulations.
By Kjeld Lauritzen, GMA Europe