You’re currently viewing the Americas website.

You’re currently viewing the Americas website.
Would you like to switch countries or language?Blast Abrasives
Topics
Waterjet Cutting
Topics
Resources
Categories
Types
Categories
Topics
Abrasive Blasting Tech Tips English Global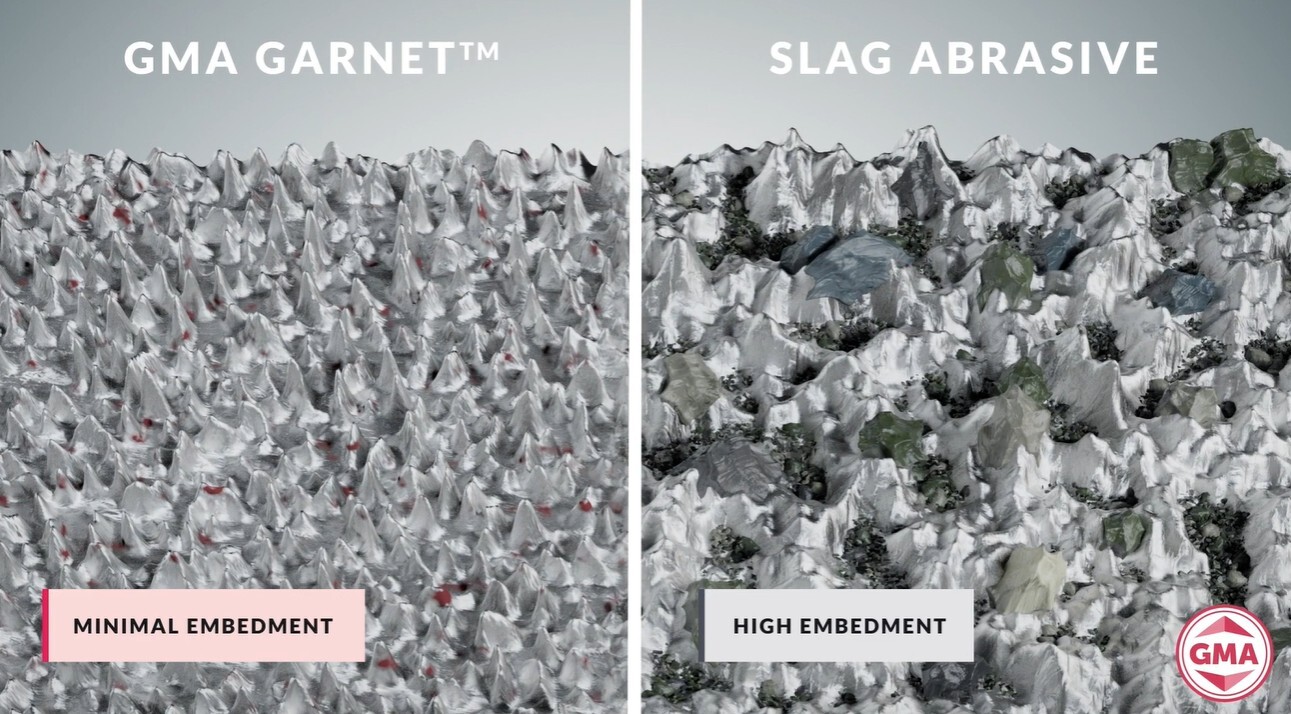
Preventing Embedment: Ensuring Surface Integrity
The Challenge of Embedment in Abrasive Blasting
Embedment occurs when abrasive particles become lodged in the surface during blasting, compromising the substrate's integrity. This can result in poor adhesion of coatings, reduced performance, and long-term failure of the protective system. For industries such as oil and gas, shipbuilding, and infrastructure, where performance is critical, understanding how to minimize embedment is essential.
Slag Abrasive: High Embedment and Inconsistent Profiles
Slag abrasives, commonly used in blasting operations, are prone to causing high embedment due to their irregular particle shapes and inconsistent quality. These abrasives often create surfaces with an inconsistent profile and low peak density. Low peak density reduces the surface area available for coatings to adhere, increasing the risk of coating delamination and system failure over time.
GMA Garnet™: Minimal Embedment and Consistent Results
Unlike slag abrasives, GMA Garnet™ is a naturally occurring mineral known for its hardness, angularity, and uniform particle size. These properties allow it to:
- Minimize Embedment: GMA Garnet™ particles efficiently remove contaminants without lodging into the substrate.
- Produce a Consistent Profile: Uniform particle size ensures a surface profile ideal for coating adhesion.
- Achieve High Peak Density: Higher peak density increases the total surface area for coatings, enhancing their durability and lifespan
By reducing embedment and ensuring a uniform surface profile, GMA Garnet™ supports better performance of protective systems across a range of industries.