Slag vs Dust
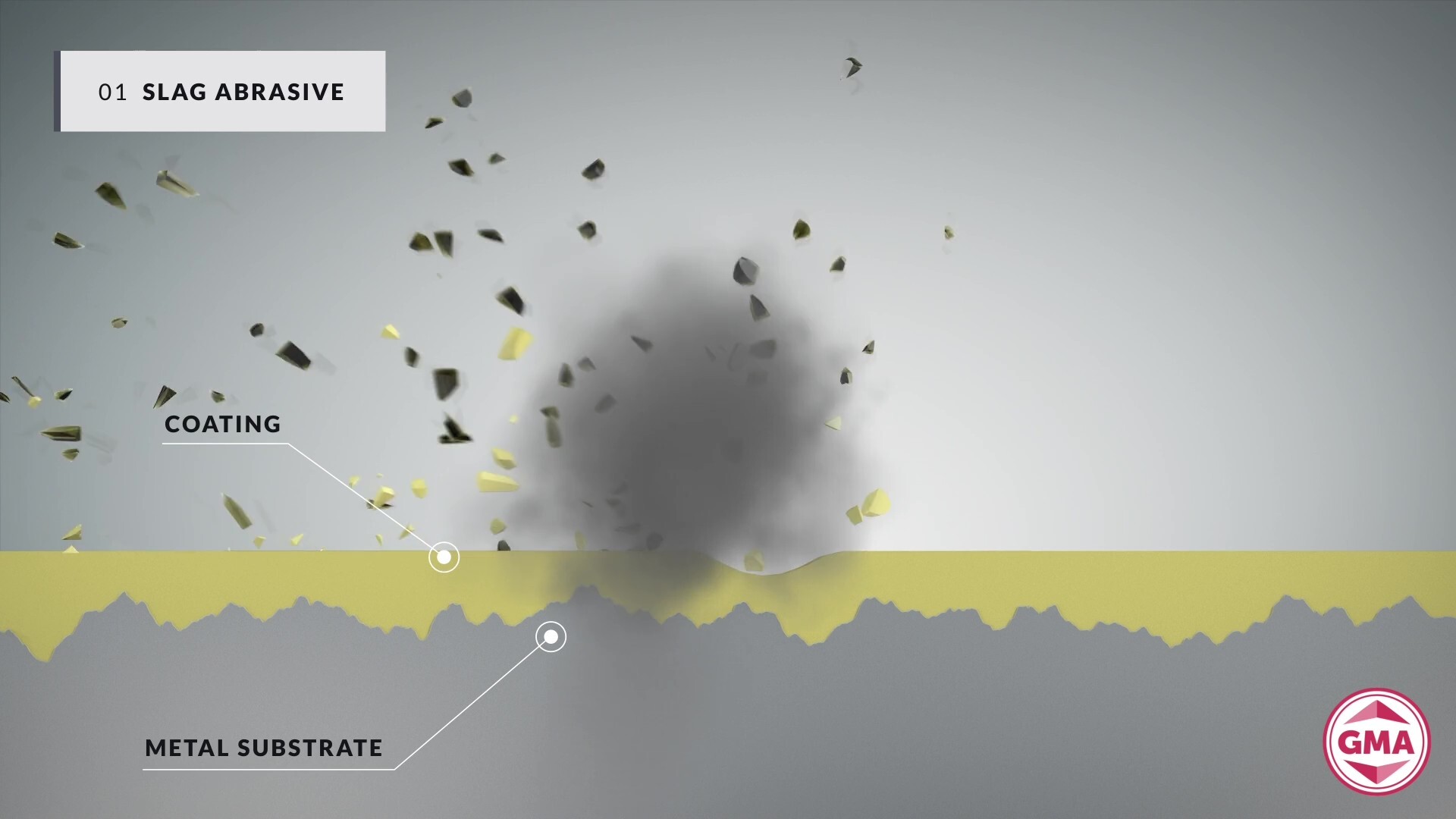
Dust generation during blasting poses significant challenges, including reduced visibility for operators, higher risks to worker health, and environmental contamination. Selecting the right abrasive can significantly reduce dust levels, ensuring a safer and cleaner worksite while maintaining surface preparation standards.
Slag abrasives are known to produce high levels of dust during blasting operations. This is due to their brittle nature, which causes them to break down into fine particles upon impact. These abrasives also tend to cause high embedment, leaving dust and debris trapped in the substrate. Combined, these factors can:
GMA Garnet™ is engineered to minimize dust generation, providing several advantages:
Subscribe to our e-newsletter for the latest news and events at GMA.