You’re currently viewing the Americas website.

You’re currently viewing the Americas website.
Would you like to switch countries or language?Blast Abrasives
Topics
Waterjet Cutting
Topics
Resources
Categories
Types
Categories
Topics
Waterjet Cutting Tech Tips English Global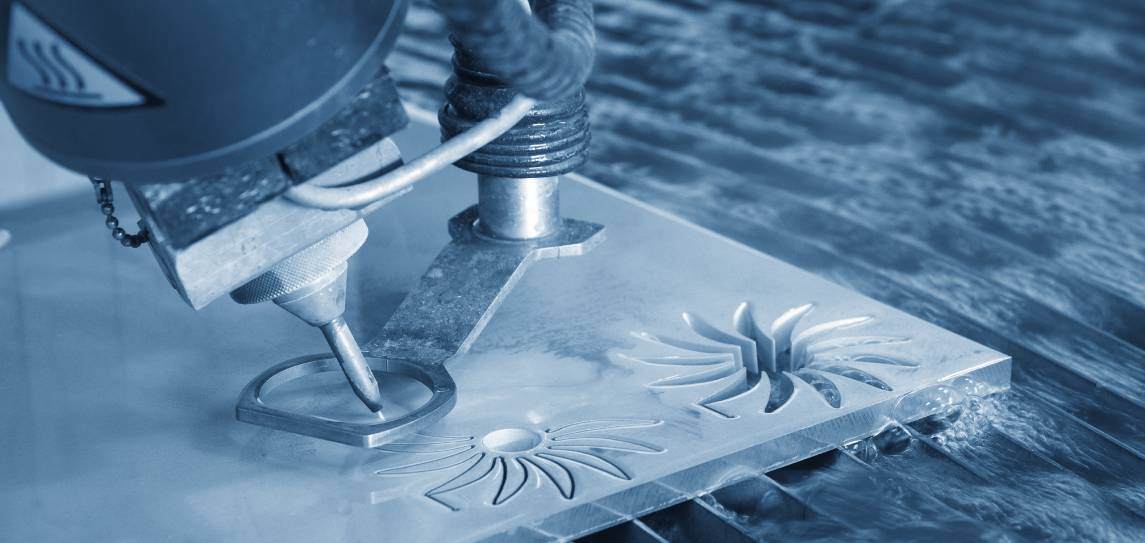
Managing taper in abrasive waterjet cutting with GMA ClassicCut™
Preventing or minimizing taper is one of the inherent production challenges in abrasive waterjet cutting. Left unmanaged, the occurrence of taper can affect the quality and precision of your cutting projects.
So, what is taper?
Taper refers to a difference in kerf width between the top, the middle and the bottom of the cut. It is a special geometrical feature that can occur in abrasive waterjet cutting processes. However, it is possible to prevent or minimize taper by managing the manual and equipment settings and selecting the right abrasive for the cutting process. Before we get into that, let’s look at the various types of taper:
V-Shaped Taper
The V-shaped taper is the most common type of taper. It creates a greater amount of kerf width at the top of the material compared to the bottom (Fig. A)
It occurs due to the loss of cutting energy when the jet stream cuts deeper into the material. This type of taper is usually associated with fast cutting – the higher the nozzle speed, the greater the risk of a V-shaped taper.
Reverse Taper
Reduced cutting speeds can produce reverse taper - creating a greater amount of kerf width at the bottom of the material compared to the top (Fig. B).
A reverse taper can occur while cutting thin materials, as it is not possible to maintain alignment between the material and the jet stream.
Barrel Taper
Barrel Taper produces the greatest kerf width in the middle of the cut (Fig. C).
It commonly occurs while cutting thick materials where the jet stream remains in the middle of the cut for an extended period to finalize the full pierce.
How to prevent or minimize taper with GMA ClassicCut™?
To prevent or minimize taper, here are some strategies:
- Use advanced waterjet cutting software
- Reduce the cutting speed
- select the appropriate nozzle sizes.
- Experienced machine operators actively control taper by adjusting the cutting speed according to the material thickness.
Besides equipment and manual fine-tuning, it is equally important that you use the highest quality garnet abrasive like GMA ClassicCut™, which is the industry standard.
The perfect combination of particle shape, density, friability and hardness of GMA ClassicCut™ abrasives is highly effective in delivering optimum performance, accuracy and the best possible edge quality with less taper (Fig. D).
Troubled by taper? Contact our technical teams today : info.global@gmagarnet.com