You’re currently viewing the Americas website.

You’re currently viewing the Americas website.
Would you like to switch countries or language?Blast Abrasives
Topics
Waterjet Cutting
Topics
Resources
Categories
Types
Categories
Topics
Waterjet Cutting Tech Tips English Global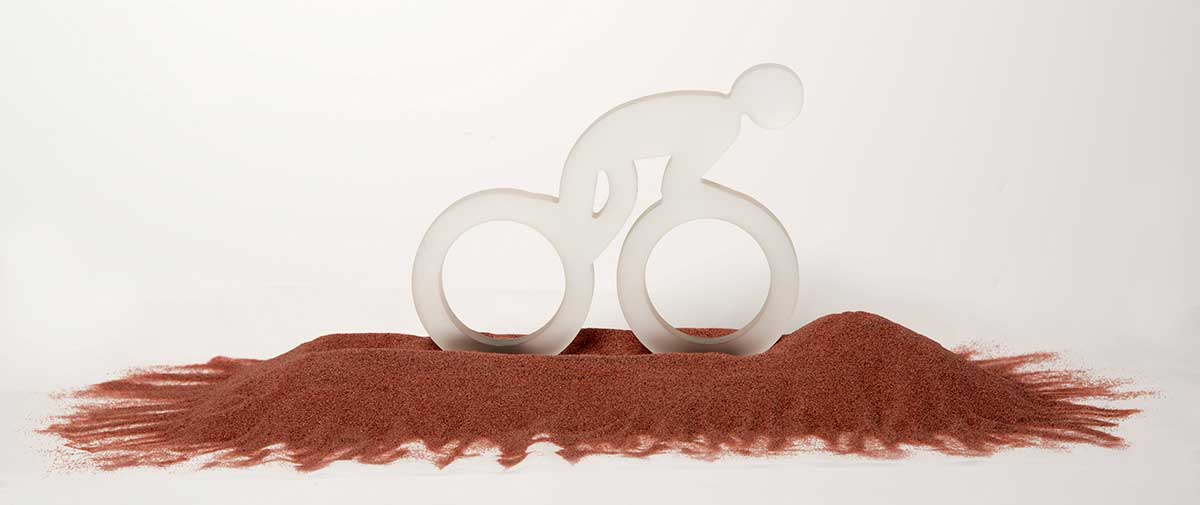
Essential tips for waterjet cutting on glass (Part II)
In the last edition, we talked about providing a strong support for the glass sheet and controlling the cutting speed to prevent the glass material from cracking or chipping. Here are two more tips:
Tip 3: Focus the Jet Stream with Finer Garnet Abrasive
Using a smaller nozzle/orifice combination, along with a finer garnet abrasive, will create a more focussed cutting stream to help prevent chipping and cracking. A more coherent stream reduces the surface area to which stress is applied, making it less likely for the glass sheet to break. A .010” ID orifice with a .030” ID nozzle, paired with GMA ClassicCut™ 120 mesh garnet, is widely and successfully used across the glass industry.
BONUS TIP
Finer abrasives provide an additional advantage for glass parts that may require polishing post cutting. Finer particles leave less striation on the cut edge, and therefore less polishing is required.
Tip 4: Proper Piercing at Low Pressure Jet Stream on Glass Sheets
Piercing the material properly is the single most important consideration when cutting glass. It is during this initial stage of the cutting process where chips or cracks are most likely to occur. Firstly, it is usually advisable to pierce the glass sheet at low pressure. The shock of a highpressure waterjet stream can easily shatter a sheet of glass. You can minimise this significantly by reducing the pressure in between 10,000 and 20,000 psi. Some trial and error may be required to determine the exact pressure required, as it varies according to the type of glass being cut.
As the pressure is reduced, it is also important to reduce the garnet abrasive flow rate to avoid clogging the nozzle. By reducing the garnet abrasive flow rate to around 0.11 kg (0.25 lbs) per minute, the water at a lower pressure can still accelerate the speed needed to pierce the glass.
BONUS TIP While piercing the material, it is critical that water and GMA Garnet™ abrasive are concurrently used by the waterjet cutting equipment. A waterjet stream which is without abrasive will not cut through the glass effectively, causing huge stress that will create cracks on the sheet. These settings can be adjusted in the waterjet control software.
While cutting glass presents unique challenges, waterjet cutting using garnet abrasives remains an extremely useful tool for the task. Across stained glass mosaics, intricate floors and tabletops inlays, and decorative ornaments, waterjet cutting has proven its worth for a wide variety of applications with GMA Garnet™.
By Chris Waters, General Manager - Waterjet Products