You’re currently viewing the Americas website.

You’re currently viewing the Americas website.
Would you like to switch countries or language?Blast Abrasives
Topics
Waterjet Cutting
Topics
Resources
Categories
Types
Categories
Topics
Waterjet Cutting Tech Tips English Global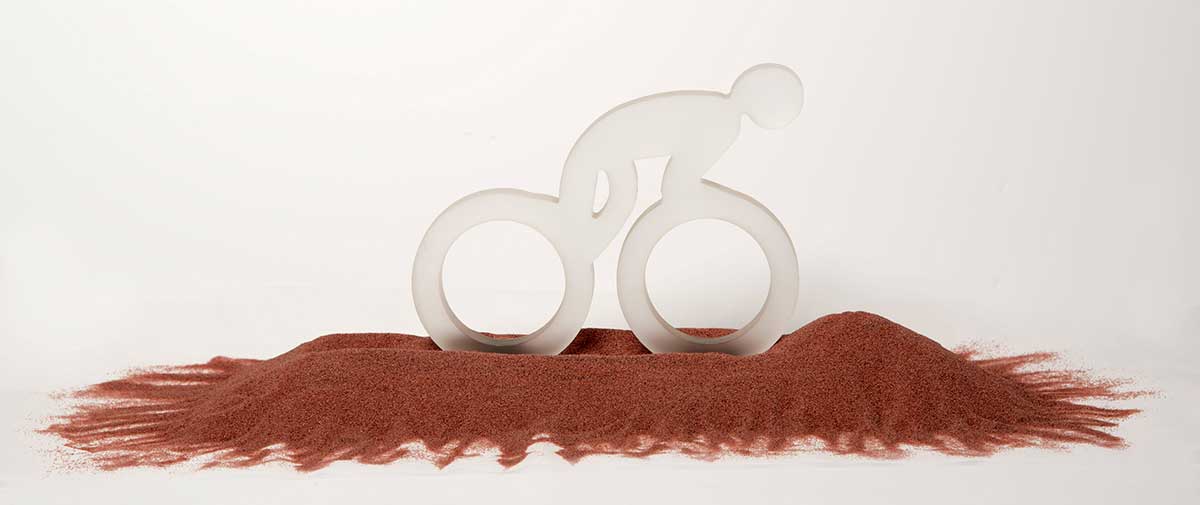
Essential Tips for Waterjet Cutting on Glass
Every material presents its own unique challenge for waterjet cutting, but few require more special considerations than glass. Compared to metals, glass cut with a waterjet machine has a higher tendency to crack or chip if not treated properly. In this article, we will discuss four essential tips to ensure an uninterrupted, high performance result for waterjet cutting of glass.
Tip 1: Strong Support for the Glass Sheet
To prevent the glass from cracking, the operator must level the entire glass sheet as precisely as possible, without gaps in between the support. Any significant difference in the elevation of the glass sheet, whether side to side or end to end, can result in torque being focused onto a small area. Cracks can subsequently form, undermining the integrity of the material.
To ensure the glass sheet is properly supported, the operator can place a sacrificial material on top of the waterjet table’s grating system. This can be something as simple as a sheet of quality plywood, or a series of polyethylene waterjet bricks. Use a spirit level to check that the material is sitting evenly before you begin cutting the glass sheet.
BONUS TIP
The sacrificial material used to support the sheet of glass will also protect the underside of the sheet from being “frosted” by garnet bouncing back from the grates below.
Tip 2: Control the Cutting Speed
Attempting to cut too quickly can prove costly when dealing with glass. The force from a vertically focused waterjet stream adds stress to the glass sheet. Usually, this stress is relieved by the cutting action itself. However, moving too quickly across a sheet of glass – particularly a thin one – may not allow the stress to be relieved fast enough, and can cause cracks to form.
BONUS TIP
While reducing speed has the potential to interfere with productivity, it is sometimes possible to compensate by stacking multiple sheets of glass to cut multiple parts at the same time.
Watch this space for more tips in the next edition.
By Chris Waters, General Manager - Waterjet Products