You’re currently viewing the Americas website.

You’re currently viewing the Americas website.
Would you like to switch countries or language?Blast Abrasives
Topics
Waterjet Cutting
Topics
Resources
Categories
Types
Categories
Topics
Waterjet Cutting Tech Tips English Global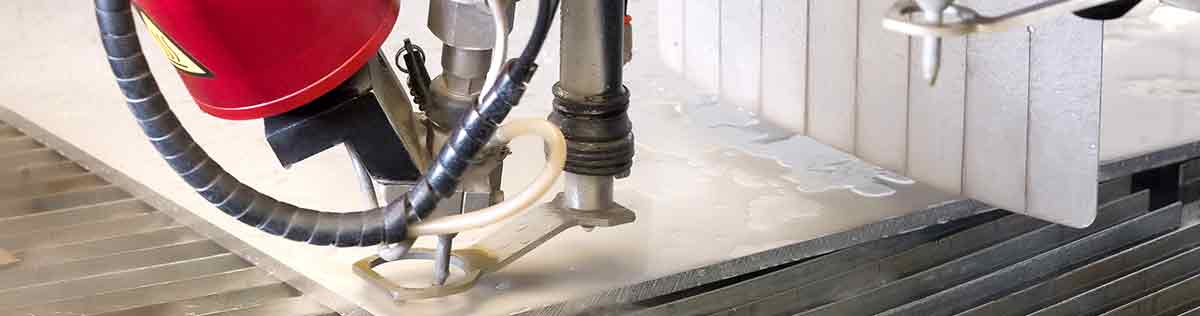
A match made in heaven (Part I)
What is waterjet cutting and how does it work?
Abrasive waterjet cutting is a (non-thermal) cold cutting process operated by a waterjet machine. Using only natural abrasive and water to cut almost any material, this process produces a smooth cutting surface with no slag or heat affected zones.
An ultrahigh-pressure pump generates a stream of water with pressure rated between 4000 to 6000 bar. The speed of the water is determined by the amount of pressure being generated. High pressure water (generally 3.8 litre per minute) flows through an orifice (made from ruby, sapphire, diamond or tetraCORE™) with a diameter between 0.10 – 0.33 mm into the cutting head, creating a jet stream of up to 1,000 m/s.
Garnet particles are fed into the focusing tube (made from tungsten-carbide) via an abrasive inlet, then introduced into the ultra-high water beam, and it becomes a powerful cutting tool, cutting up to 300 mm thick metal into any shape.
Waterjet cutting equipment offers incredible flexibility that can be easily adjusted for a specific cutting requirement.
Why is garnet used as an abrasive in waterjet cutting instead of other substitutes?
Over the last 30 years, both natural and synthetic abrasives have been considered for use in waterjet cutting. Almandine garnet has been identified as the most suitable mineral for waterjet cutting due to its unique characteristics, high performance and overall profitability of the operation.
Abrasives that are softer than garnet, such as olivine or glass, provide a long mixing tube life but do not ensure fast cutting speed. As for abrasives that are harder than garnet, such as Aluminium Oxide or Silicon Carbide, these materials cut faster than garnet but do not provide a high cutting-edge quality. The life span of the mixing tube is also shortened by up to 90% in comparison to garnet.
In addition, garnet is also environmentally friendly as its waste can be repurposed as a filler in asphalt and concrete products. High quality abrasives such as GMA Garnet can be recycled up to five times.
What performance do you expect from an abrasive waterjet cutting machine?
In CNC manufacturing, there are many ways to cut materials. Computers are used to control machine tools to perform cutting applications. While CNC laser cutting and plasma cutting are quite popular and offer a faster speed in cutting materials like steel, aluminium and copper up to 20mm in thickness, these methods often fall short when extreme precision and flexibility are required.
Waterjet cutting, on the other hand, can be used to cut anything from soft rubber and plastics to the hardest metals and ceramics without any heat affected zones.
You can also increase the capacity by mounting two or three cutting heads on the cutting table. These will follow the same contour in parallel, from 2D to advanced five-axis cutting in 3D.
In the next edition, we will be talking about the material type and thickness, and the choice of garnet.
By Kjeld Lauritzen, Sales Manager