You’re currently viewing the Americas website.

You’re currently viewing the Americas website.
Would you like to switch countries or language?Blast Abrasives
Topics
Waterjet Cutting
Topics
Resources
Categories
Types
Categories
Topics
Abrasive Blasting Tech Tips English Global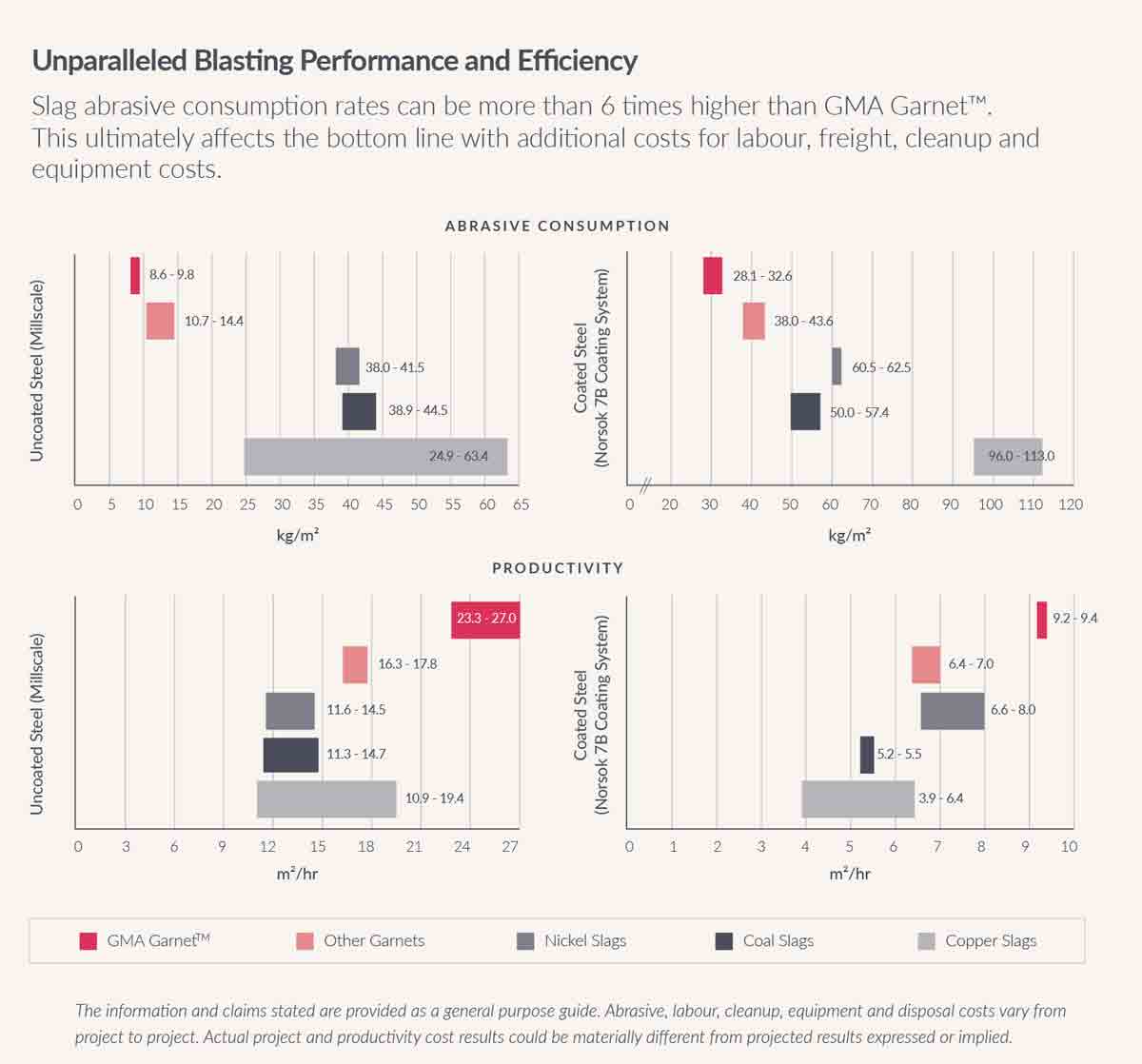
Improving onsite blasting efficiency
I’m sure at some stage recently shopping for a new car or washing machine there is a good chance that you’ve conducted a side-by-side comparison of different makes and product types on websites, read reviews by others or looked at the side-by-side specs to help you make the decision on which one will suit your needs.
When it comes to specialist products like blast abrasives, it’s not always easy to find data outside of anecdotal information and vague facts. It’s not an easy feat to conduct performance testing when it comes to blast abrasives as you have multiple variables such as equipment optimisation, abrasive performance, blasting technique and knowledge; as well as the environment of the blasting operations, the substrate and coating to be removed.
Product comparisons take a good mix of product features, performance specifications and price points. Price isn’t always a good indicator. Sometimes it’s difficult to understand when products may be substantially lower in price doesn’t always mean that they will perform well compared to other higher priced alternatives.
At GMA, we are always looking at ways to understand how our products perform against others and help understand how we can do better and provide a product optimised to your needs. Recently, GMA has conducted performance testing in the United States, Australia and Europe to better understand how our products perform against others.
Onsite Performance Testing: Proof of Concept
It’s important to note that performance testing does not change the fact that on-site product testing and trials are still required and a low-risk approach to proof of concept, making sure the product fits your needs. Testing a product in a controlled environment with vendors, contractors, and asset owners provides real-time, practical results on your blast abrasive performance.
Due to the complexity of equipment and abrasive choice, on-site trials are invaluable for assessing product quality, productivity, consumption, environmental performance, as well as health and safety parameters. Additionally, on-site trials allow technical personnel to help optimise results through best practices in product selection and reduce overall project costs.
A trial will help you see first-hand how the products perform against other brands and iron out any issues before critical turnaround requirements or plant shutdowns. You do not want surprises.
At GMA, we have developed a comprehensive onsite trial performance procedure that captures the right data and information. The procedure covers all avenues of the performance testing that is conducted on your site, based on your specification and application and comparison products that you would like to compare. GMA’s Technical Sales team also provides a comprehensive report for review and discussion afterwards.
European Performance Testing
Late in 2021, the European Blast Team developed a Performance Testing Procedure for an in-depth product comparison trial to fully understand how GMA Garnet™ performs against common slag abrasives.
The team engaged an independent blasting contractor and third-party consultant to help verify up to 20 different performance criteria on surface results (profile and soluble salts through to productivity and consumption), dust and air monitoring analysis.
GMA being a global abrasive supplier, work on regional requirements, and a one size fits all doesn’t always suit. Regional abrasive equipment, abrasive products and blasting techniques are not always the same, so local testing on local equipment and products is important to best understand local performance.
With an adjusted approach for all abrasives tested, the blasting and equipment are optimised for the best results from all abrasives tested. The abrasives were tested on bare steel (milscale) and also on cured coated abrasives over a couple of weeks.
Among the popular European brands tested were three Copper Slag Abrasives, one Coal Slag and one Nickel Slag. GMA products include GMA PremiumBlast™ and GMA NewSteel™ garnet - the results were surprising.
Productivity
On average productivity for:
- GMA Garnet™ was 60% higher than Copper Slags
- GMA Garnet™ was about double compared to the Nickel and Coal Slags tested.
Consumption
On average consumption for:
- Copper Slags was about 2 ½ higher on average for the three Copper Slags tested compared to GMA Garnet™ products.
- Nickel and Coal Slags were about 3 ½ times higher than GMA Garnet™ products.
- The combination of productivity and consumption is also dependent on the grain size. At GMA we engineer our blends wider grain distribution than most other blast abrasive products. The a wider distribution of coarse and fine particles enable to ‘cut’ through coatings and create a profile. The finer particles are able to ‘clean’ the surface right into the valleys without compromising the overall profile. Hence the term ‘cut and clean.’
Though GMA Garnet™ has a higher upfront cost compared to typical Slag abrasives, its considerable higher productivity and lower consumption have a significant bearing on the overall project costs.
Coupled in other significant costs such as additional abrasives, transport costs, cleanup costs for using Slag abrasive, the reduced time spent on blasting is a substantial time saving solution by using GMA Garnet™.