You’re currently viewing the Americas website.

You’re currently viewing the Americas website.
Would you like to switch countries or language?Blast Abrasives
Topics
Waterjet Cutting
Topics
Resources
Categories
Types
Categories
Topics
Abrasive Blasting Tech Tips English Global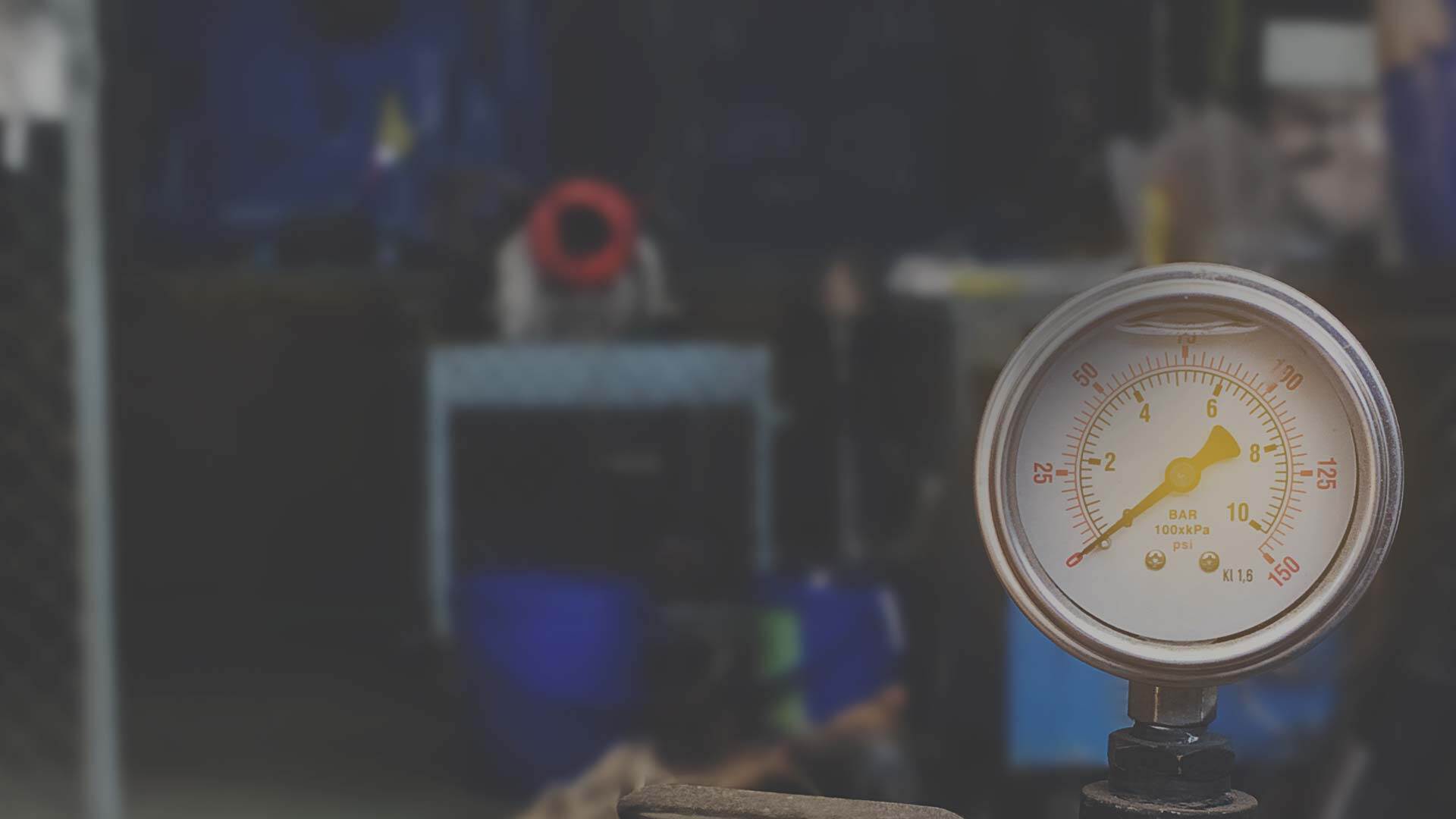
How to Maximize Efficiency in Abrasive Blasting [Guide] | GMA Garnet
Using properly adjusted and maintained abrasive blasting equipment and correct grit blasting techniques can reduce your blasting time and increase the quality of the finished surface.
Here's how.
Adjusting Abrasive Blasting Equipment for Maximum Performance
1. Use the correct air pressure for abrasive blasting.
Optimum abrasive blasting pressure is at least 100 psi. If you use lower pressures, productivity will almost certainly be reduced. Measure air pressure at the nozzle, rather than at the compressor, because there will be an unavoidable drop in pressure between the compressor and the nozzle, especially when you use long hose lengths. Measure nozzle pressure with a hypodermic needle gauge inserted into the blast hose, directly before the nozzle.
2. Use the correct blast hose for the job.
Always use good quality blast hose and select the correct diameter to minimize friction losses.
A rough guide to sizing is that the blast hose diameter should be between three and five times that of the nozzle. Hose lengths should be kept as short as site conditions will allow and correctly sized couplings fitted to avoid unnecessary pressure loss throughout the system.
3. Use the correct blast nozzle.
The size of the blast nozzle orifice will affect the productivity of the blasting operation. The larger the bore, the bigger the area blasted, facilitating faster production rates. However, to achieve the desired surface finish, the volume and pressure of the air supply needs to be high enough to ensure that abrasive velocity is maximized.
There needs to a balance between compressor, hose and nozzle sizes. There are standard tables available from abrasive blasting equipment manufacturers that indicate appropriate nozzle and compressor sizes. Nozzle type also affects the blast pattern and productivity. Straight bore nozzles produce a narrow blast pattern, commonly used for spot blasting.
Venturi nozzles produce a wider pattern along with increased abrasive velocity, facilitating higher productivity. Regularly inspect blast nozzles and replace them if necessary. The nozzle liner will become worn over time and the resultant increased orifice size will require more air in order to maintain nozzle pressure and abrasive speed.
4. Check your air supply.
You need a cool, dry air supply to transport the abrasive through the blast hose and propel it onto the surface to be cleaned. Damp air can cause agglomeration of the abrasive and blockages in the hose. It can also cause moisture to condense on the substrate, leading to possible coating failure due to blistering.
The air supply should also be free from compressor oil, as this could contaminate the abrasive and subsequently the cleaned surface.
5. Check your abrasive metering valve.
The metering valve is a critical part of the abrasive supply to the nozzle. This valve precisely controls the amount of abrasive introduced into the airstream.
Excess abrasive causes the particles to collide with each other, reducing velocity and ultimately affecting the quality of finish.Too little abrasive will produce an incomplete blast pattern resulting in reduced productivity because of some areas needing a redo.
What to look for in equipment setup:
- Compressor capable of supplying air at the required pressure and volume
- Blast nozzle balanced with available air supply
- Precise and repeatable abrasive metering valve
- Correctly sized blast hose rated at the relevant working pressure
The design of your abrasive blasting equipment can have a major influence on the surface preparation condition obtained and on the efficiency of the blasting process. You need to use the correct blast pressure, abrasive supply, nozzle type and blasting technique to ensure the steel surface meets the desired specification and you minimize costs.
Employing Grit Blasting Techniques for Optimum Performance
While how you set up your equipment is essential, equally important is the abrasive blasting procedure you employ.
1. Maintain the correct distance.
To achieve the best blast pattern and profile on a surface while maintaining productivity, keep the abrasive nozzle at an appropriate distance from the work surface.
Being too close to the surface will produce a narrow blast pattern, and it will take longer to prepare the area.
Holding the nozzle too far from the surface can result in poorer cleaning and the required profile might not be obtained.
For garnet blasting, the stand-off distance is ideally 46 cm (18 in) (although this can depend on the type of nozzle used).
2. Maintain the correct blast angle.
The angle of blasting can affect the productivity depending on the original state of the surface.
In general, a 90-degree angle will cause the abrasive to rebound, leading to reduced performance. However, in extreme cases, such as heavily rusted or pitted surfaces, angles between 80 and 90 degrees may prove to be most effective.
Too narrow an angle could cause the abrasive to skim across the surface, resulting in reduced profile.
When removing old paint, 45 to 60 degrees is typical, and for general cleaning it is 60 to 70 degrees.
When garnet blasting, the most effective angles tend to be between 55 and 70 degrees, depending on the nature of the substrate.
3. Use an even, overlapping sweeping action.
The time spent cleaning any particular spot or area varies depending on the operation. It can be short when removing loose materials but considerably longer for tightly adherent material.
To ensure consistent levels of cleanliness and surface profile, use an overlapping sweeping motion. Use a steady movement and don't dwell unnecessarily on any particular area.
4. Check the surface profile meets the requirements of the specification.
Check the blasted surface profile to ensure that it complies with the relevant specification. You can do this by utilizing Testex Tape in conjunction with a spring micrometer or by using a digital profile meter.
5. Ensure that operators are properly trained.
Blast operatives should have knowledge of best practices and understand the value of good surface preparation. Most importantly however, they should be properly trained in job requirements, safety and abrasive blasting procedure.
Start Today
Maximize your garnet blasting with GMA. Investing in high quality garnet abrasives such as GMA Garnet™ will enhance the performance of your abrasive blasting procedure. Contact us to learn more.