You’re currently viewing the Americas website.

You’re currently viewing the Americas website.
Would you like to switch countries or language?Blast Abrasives
Topics
Waterjet Cutting
Topics
Resources
Categories
Types
Categories
Topics
Waterjet Cutting Our Customers English Global Sustainability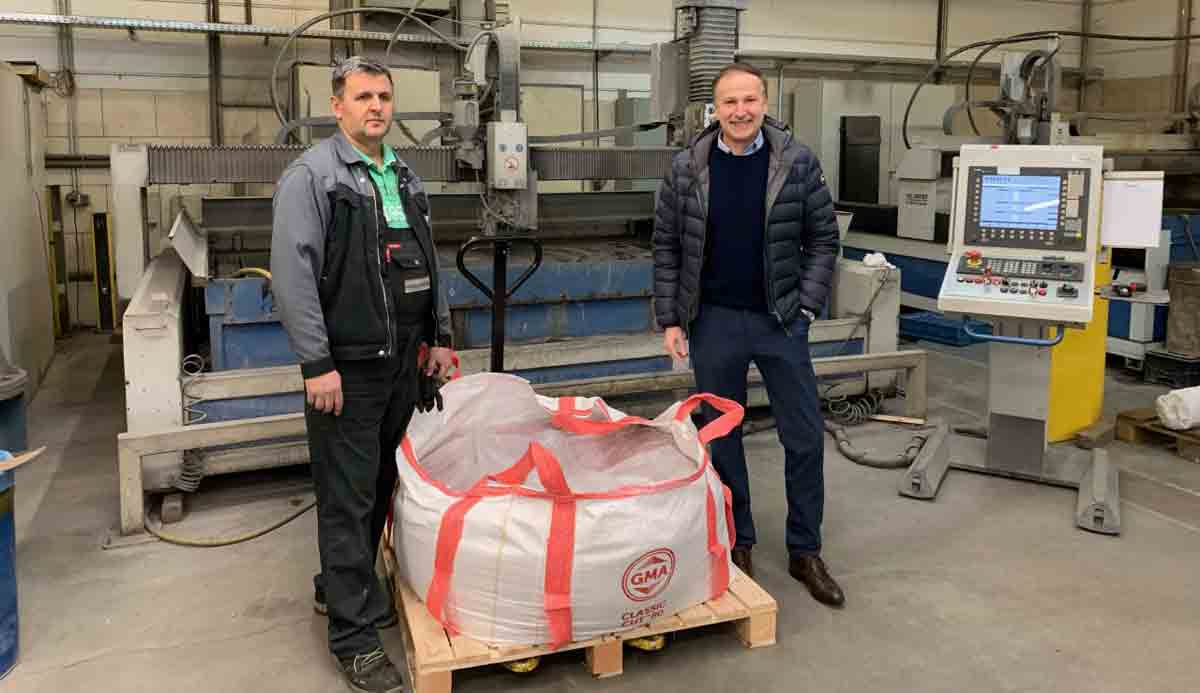
German sheet metal fabricator cuts cost and increases productivity by 33%
Further cost savings include lower abrasive consumption and disposal costs
Osthaus & Beckert (O&B) is a well-known and respected sheet metal working company in Schwanewede, north of Germany.
The company offers modern sheet metal forming and development work for highly specialized industries such as automotive, aviation, aerospace, handcraft and shipbuilding. These materials are produced using transformation (edging, rolling, tube bending), welding, chipping and deburring methods and laser and waterjet cutting technologies. O& B has been cutting a wide range of materials since 2000.
With the rising cost of production in Germany and across Europe, the company was keen to explore and implement cost-saving opportunities in their processes, such as abrasive and used garnet disposal options in the waterjet cutting division.
Early this year, the GMA waterjet team conducted a cutting test on site to compare the speed and consumption rate between GMA ClassicCut™ 80 garnet and Chinese garnet. Using a Waricut machine made by Ridder, both products were used to cut a 20mm thick stainless material at 3,700 bar with the same cutting edge quality.
The performance data revealed that GMA ClassicCut™ 80 cuts 33% faster and uses less abrasives - abrasive consumption was reduced by 30% compared to Chinese garnet.
Since the cutting test, O&B was convinced that by using high quality GMA Garnet™ abrasives, the increased productivity and lower abrasive consumption would reduce their overall cost of production. Furthermore, the company accrues further cost savings from a sustainable used garnet disposal solution offered by GMA Europe.
O&B Manager – Waterjet Cutting Holger Gätjen was very satisfied with the quality of GMA Garnet ClassicCut™ 80 and the service support by GMA Europe.
“Now, we are able to use the combination of 0,25 mm water orifice, 0,76 mm inside diameter of focusing tube and GMA ClassicCut™ 80 without any blockages at the nozzle,“ Mr Gätjen said.
50mm steel work piece cut with GMA ClassicCut™ 80.
Mr Gätjen is also happy to use tetraCORE orifices. Paired with GMA Garnet ClassicCut™ 80, it guarantees a product life of 400 hours.
O & B is now cutting 33% faster and consuming 30% less abrasive with reduced disposal costs. You can make these changes to your operations and start saving too. Write to us at info.global@gmagarnet.com