You’re currently viewing the Americas website.

You’re currently viewing the Americas website.
Would you like to switch countries or language?Blast Abrasives
Topics
Waterjet Cutting
Topics
Resources
Categories
Types
Categories
Topics
Waterjet Cutting News English Global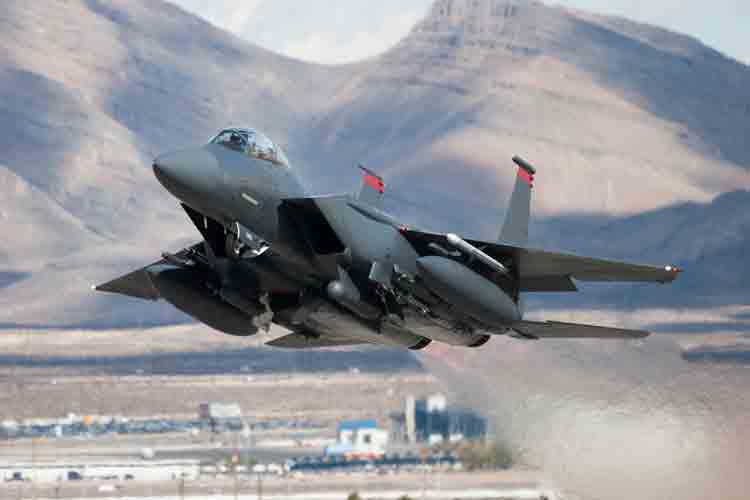
Challenges in cutting Aerospace & Defense components as the market recovers
The year 2022 is crucial for the Aerospace and Defense industries to adjust their operations and supply chain to run as efficiently as possible. With commercial air travel and customer order activity in a much better shape than earlier post-COVID expectations, the global aerospace and defense market is expected to grow from USD 700 billion in 2021 to over USD 750 billion in 2022 at a compound annual growth rate (CAGR) of 7.8%1.
The growth is mainly due to companies rearranging their operations and recovering from the COVID-19 impact.
As the industries recover, the demand for parts and components rises and manufacturing these parts requires substantial time and effort. Aerospace components are typically made from advanced and expensive materials that are difficult and time-consuming to produce, such as rotary blades, wing and tail sections of an aircraft and high temperature resistant alloys. These components are made of 6061 grade aluminum, titanium, composites, titanium alloys, nickel-based super-alloys, special steels and heat resistant ceramics.
The main challenges of manufacturing high precision components are sourcing materials via a secure supply chain to ensure consistency in material supply and quality and running a cost-effective production and cutting method. Abrasive waterjet is well known in the industry to be the ideal cutting method that meets the highest quality requirements as it is inherently a cold cutting process. The global waterjet cutting machine market size is projected to reach USD 1.6 million by 2027, exhibiting a CAGR of 6.3% in the forecast period (2020-2027)2
The environmentally friendly cutting method does not create Heat-Affected Zones, which is a major requirement among aircraft manufacturers. Hot process methods such as laser cutting can easily damage the primary material by overheating the structure and/or the integrity of alloys or super-alloys. It is not allowed for cutting structural or flight safety critical net shape parts. As no heat is produced during the waterjet cutting process, micro cracks and oxide inclusions do not occur.
Another key advantage of waterjet cutting is the separation process which is not limited by material thickness.
While other cutting methods may potentially lose performance and edge quality from 2 inches onwards (for certain materials), waterjet cutting can cut through titanium, Kevlar and very thick stainless steel.
Moreover, you will not get burrs and rough edges and cut complex shapes easily while minimizing the need for secondary finishing processes due to its excellent surface finish. Reduced waste materials and increased productivity are crucial factors in driving the recovery and development of these industries.
Strict requirements on high precision components manufacturing will also always be a challenge for manufacturers, suppliers and subcontractors. The use of high-quality garnet abrasive correlates to the required cutting accuracy, speed and edge quality. A constant waterjet flow with the purest and highest quality garnet is needed to achieve a high precision edge.
GMA Garnet™ abrasives consist of the highest quality alluvial garnet engineered to achieve optimum performance, accuracy and cutting speed. Its particle shape, density, toughness (low friability) and hardness are ideal for maximizing your cutting process to achieve high productivity and precision edge quality. GMA Garnet™ is the ideal abrasive for running abrasive waterjet systems at peak performance.
1. Global News Wire: https://www.globenewswire.com/news-release/2022/02/28/2392765/0/en/Aerospace-Defense-Global-Market-Report-2022.html
2. Fortune Business Insights: https://www.fortunebusinessinsights.com/waterjet-cutting-machines-market-102026