You’re currently viewing the Americas website.

You’re currently viewing the Americas website.
Would you like to switch countries or language?Blast Abrasives
Topics
Waterjet Cutting
Topics
Resources
Categories
Types
Categories
Topics
Abrasive Blasting Tech Tips English Global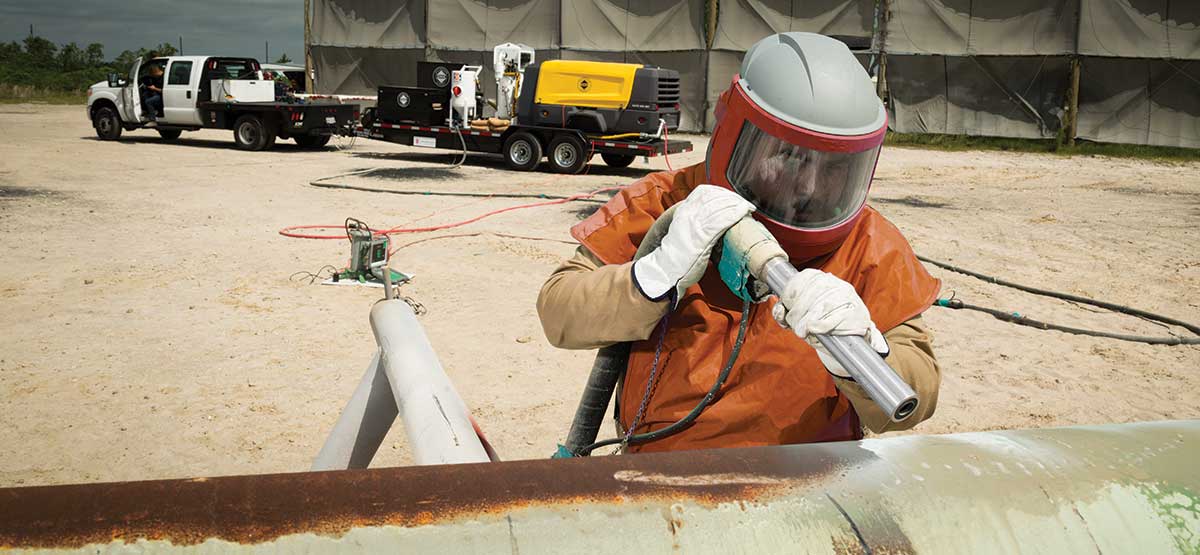
The Importance of Moisture Removal
Dry compressed air is an absolute necessity for efficient, smooth and reliable blasting operations.
Moisture in blasting systems is regularly ignored, resulting in negative flow-on effects which are often wrongly considered by the operator as operational issues to be managed “as-best–as– possible” with existing equipment.
Proper selection of effective and suitable moisture removal equipment is highly recommended for most commercial dryblasting operations, and becomes a particularly important system component in high-humidity environments.
There are a number of inefficiencies and issues that arise from excessive moisture levels in compressed air used for abrasive blasting:
- Moisture and condensation left in the system causes damage to the valves, fittings and pot.
- Wet abrasive does not flow well, causing spitting or irregular abrasive volume exiting the nozzle.
- Using the choke valve to improve abrasive flow causes inter-particle collisions in the blast hose. This leads to in excessive consumption, higher energy requirements, reduced impact speed and slowed cleaning rates.
- Moisture exiting the nozzle can cause flash rusting of the substrate.
Conversely, an effective moisture removal system will provide several benefits:
- Compressed air that is lighter and easier to propel, which means less energy is required.
- Smoother abrasive flow and ability to reduce the feed rate, which reduces consumption and wastage.
- Less downtime and fewer equipment maintenance requirements, reducing unnecessary disruptions.
- The superior performance of GMA Garnet is maximized, further reducing the true cost per m2, when compared with less effective abrasives such as slags, softer mineral abrasives and sands.
In summary, the benefits of selecting a moisture removal tool that is suited to a particular blasting system, will significantly improve the efficiency and reliability of your blasting operation. Depending on selected equipment, effective moisture removal can reduce garnet consumption by up to 20%, as well as increasing blasting speeds by up to 10%.
For more information and recommended equipment, please contact your local GMA technical consultant to determine suitable equipment options that will benefit and optimise your operational profitability.
By Marc Putzier, GMA Asia Pacific
International Sales & Technical Manager NACE Coating Inspector, Level 2 Certified
*Note: These recommendations are to be implemented at the user’s discretion and deemed fit for their operating environment. In no event will GMA be responsible for expected performance or damages of any nature whatsoever resulting from the use of or reliance upon information presented here.