You’re currently viewing the Americas website.

You’re currently viewing the Americas website.
Would you like to switch countries or language?Blast Abrasives
Topics
Waterjet Cutting
Topics
Resources
Categories
Types
Categories
Topics
Abrasive Blasting Tech Tips English Global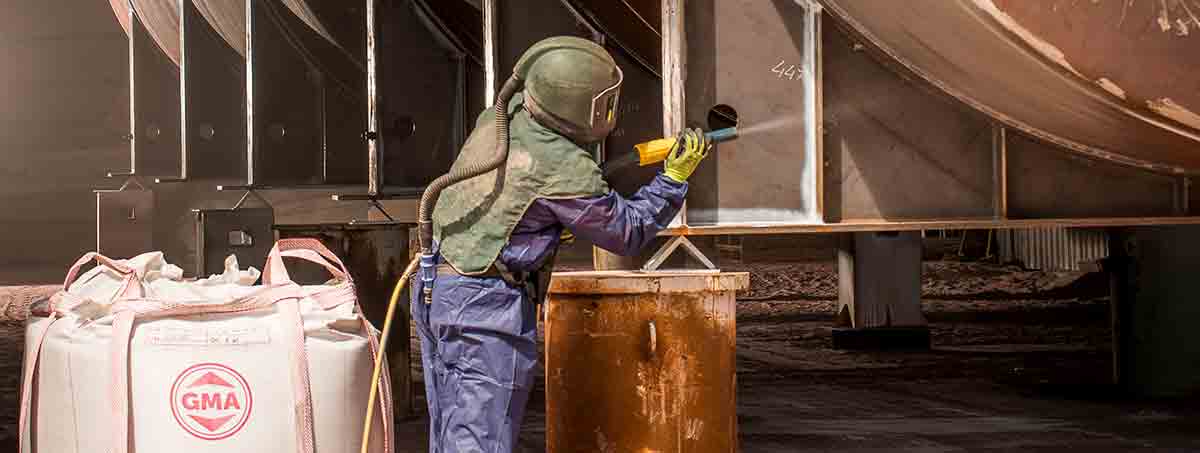
The ABC of Abrasive Blasting - Part B
Throughout the world, GMA Garnet™ is used as a blast cleaning abrasive across a wide variety of industries. The three-part guidelines on blasting tips and techniques will enable you to achieve a more efficient and effective blast operation.
Part B – Maximising the efficiency of the blasting operation
B1 - Ensure that the correct air pressure is used.
Optimum blasting pressure is at least 100 psi. If lower pressures are used, productivity will almost certainly be reduced.
Air pressure should be measured at the nozzle, rather than at the compressor, as there will be an unavoidable drop in pressure between the compressor and the nozzle, especially when long hose lengths are used.
Nozzle pressure should be measured with a hypodermic needle gauge inserted into the blast hose, directly before the nozzle.
B2 – Use the correct blast hose for the job.
Good quality blast hose should always be used and the correct diameter selected in order to ensure that friction losses are minimised.
A rough guide to sizing, is that the blast hose diameter should be between 3 and 5 times that of the nozzle. Hose lengths should be kept as short as site conditions will allow and correctly sized couplings fitted in order to avoid unnecessary pressure loss throughout the system.
B3 – The blast nozzle.
The size of the blast nozzle orifice will affect the productivity of the blasting operation. The larger the bore, the bigger the area blasted, facilitating faster production rates.
However, in order to achieve the desired surface finish, the volume and pressure of the air supply needs to be high enough to ensure that abrasive velocity is maximised.
Hence, there needs to a balance between compressor, hose and nozzle sizes.
There are standard tables available from equipment manufacturers which indicate appropriate nozzle and compressor sizes.
Nozzle type also affects the blast pattern and productivity. Straight bore nozzles produce a narrow blast pattern, commonly used for spot blasting.
Venturi nozzles produce a wider pattern along with increased abrasive velocity, facilitating higher productivity.
Blast nozzles should be regularly inspected and replaced if necessary. The nozzle liner will become worn over time and the resultant increased orifice size will require more air in order to maintain nozzle pressure and abrasive speed.
B4- Air supply.
A cool, dry air supply should be used to transport the abrasive through the blast hose and to propel it onto the surface to be cleaned. Damp air can cause agglomeration of the abrasive and blockages in the hose. It can also cause moisture to condense on the substrate, leading to possible coating failure due to blistering.
The air supply should also be free from compressor oil, as this could contaminate the abrasive and subsequently, the cleaned surface.
B5/B6 – Abrasive metering valve.
The metering valve is a critical part of the abrasive supply to the nozzle. This valve precisely controls the amount of abrasive introduced into the airstream.
Too little abrasive will produce an incomplete blast pattern resulting in reduced productivity, because of some areas needing to be re-done.
Excess abrasive causes the particles to collide with each other, reducing velocity and ultimately affecting the quality of finish.
What to check for in equipment set-up:
Compressor capable of supplying air at the required pressure and volume.
Blast nozzle balanced with available air supply. Precise and repeatable abrasive metering valve.
Correctly sized blast hose rated at the relevant working pressure.
The design of your blasting equipment can have a major influence on the surface preparation condition obtained, and on the efficiency of the blasting process. The correct blast pressure, abrasive supply, nozzle type, and blasting technique must be used to ensure the steel surface meets the desired specification and the costs are minimised.
By John Halewood, GMA Group