You’re currently viewing the Americas website.

You’re currently viewing the Americas website.
Would you like to switch countries or language?Blast Abrasives
Topics
Waterjet Cutting
Topics
Resources
Categories
Types
Categories
Topics
Abrasive Blasting Tech Tips English Global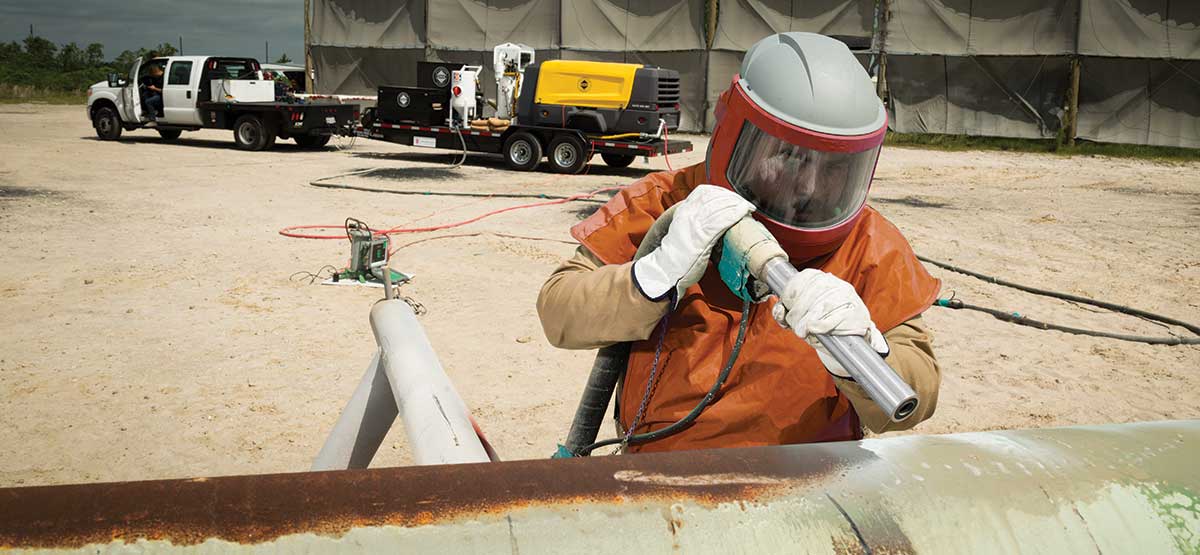
Six tips for maximising the efficiency of your blasting operation
The design of your blasting equipment can have a major influence on the surface preparation condition obtained, and on the efficiency of the blasting process. The correct blast pressure, abrasive supply, nozzle type, and blasting technique must be used to ensure the steel surface meets the desired specification and the costs are minimised.
These six tips will allow you to attain the most efficient and effective blast operation with all GMA Garnet™ abrasives.
1. Optimal pressure is instrumental to success
- Pressure at the blast nozzle should be set at a minimum of *100 psi.
- Blasting efficiency drops 1.5% for every 1 psi below 100.
- When attaching additional equipment, the compressor should be sized appropriately to maintain sufficient air pressure at every nozzle (minimum 100 psi).
2. Proper valve control ensures optimal garnet consumption
- Having the right abrasive metering valve is crucial. Avoid using a ball, flat or pancake metering valve.
- Open and close the valve by a few turns to ensure accurate metering. Test production rate by blasting on the surface.
- The right abrasive metering can help reduce garnet consumption by 25%.
3. Use a partner to achieve optimal blast results
Have a separate person adjusting the metering valve in line with the blaster’s instructions.
- Hearing a chugging sound means too much abrasive is being used.
- The abrasive exiting the nozzle should be almost invisible.
4. Nozzle size and its condition affects blast efficiency
- Nozzle sizing should be dependent on project specification and air availability.
- A small increase in nozzle size will result in a large increase in air and abrasive consumption.
- Check for nozzle wear with a nozzle-sizing gauge prior to each shift. Replace nozzle when it is worn to 2mm of its original size.
5. Blast with cool, dry compressed air
- Cool, dry compressed air blasts up to 15% faster.
- Increased moisture can increase garnet consumption by 25% or more.
6. Shorter air supply hose and the correct hose size will minimize pressure drops
- Minimum diameter for air supply hose
– 4 times the blast nozzle orifice.
- Minimum diameter for blast hose
– 3 times the blast nozzle orifice.
- Maximum diameter for blast hose
– 5 times the blast nozzle orifice.
*If you are not achieving a minimum 100 psi at the nozzle, it's important to check your entire blasting system and locate the pressure loss. Check the pressure out of the compressor, into the dryer, out of the dryer, into the pot and out of the pot with the needle gauge to ensure an optimal blasting operation.
By Kevin Zimont, GMA Americas