You’re currently viewing the Americas website.

You’re currently viewing the Americas website.
Would you like to switch countries or language?Blast Abrasives
Topics
Waterjet Cutting
Topics
Resources
Categories
Types
Categories
Topics
Abrasive Blasting Tech Tips English Global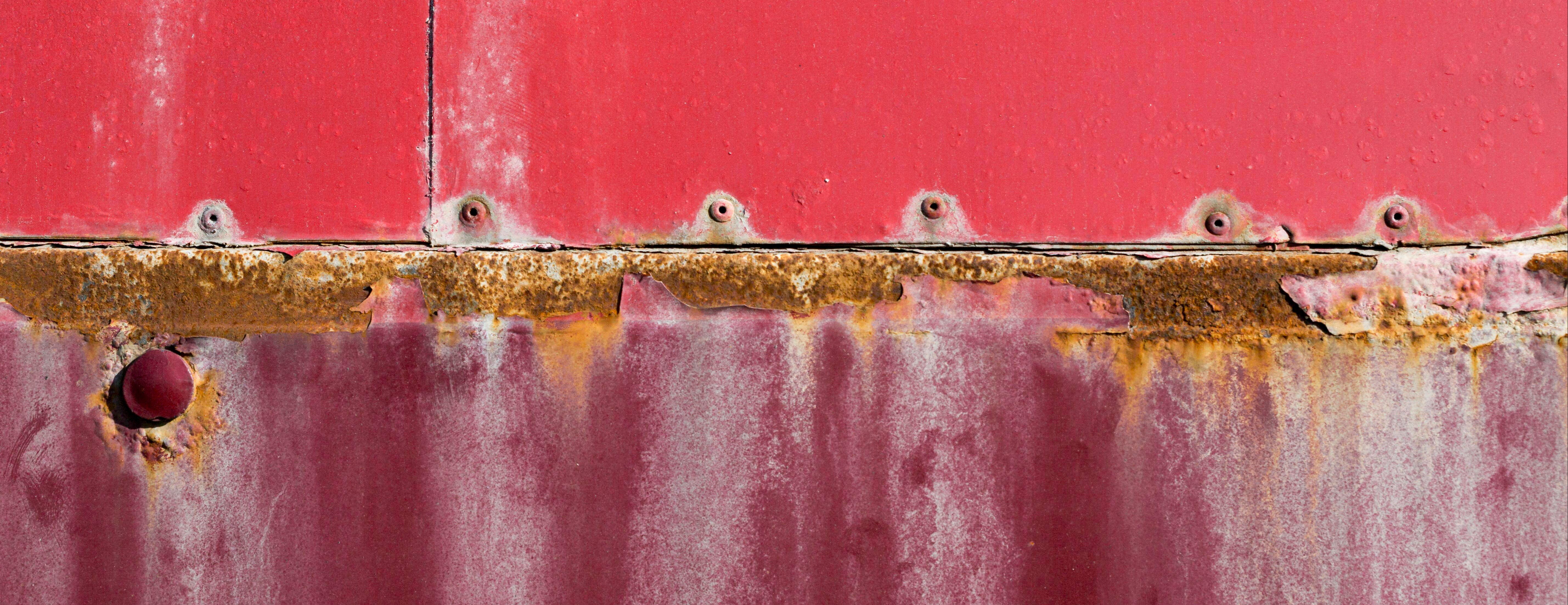
Corrosion and the Benefits of Abrasive Blasting
The Global Cost of Corrosion
Corrosion costs the global economy an estimated US$2.5 trillion each year—impacting infrastructure, industry, and safety worldwide. It’s a persistent challenge that affects everything from pipelines and bridges to ships and storage tanks. The good news? With the right surface protection strategies in place, a significant portion of these costs can be prevented.
Why Coatings Alone Aren’t Enough
Protective coatings are one of the most widely used and cost-effective solutions for combating corrosion. When applied correctly, they form a barrier between metal surfaces and environmental exposure—blocking out moisture, chemicals and air. However, even the most advanced coating systems can fail if the surface underneath isn't properly prepared.
“Inadequate surface preparation often leads to costly repairs and reduced coating durability, making optimal surface cleanliness and peak density essential for effective adhesion”
Pete Mitchell
VP of New Market Development and Technical Management, GMA Garnet Group
The Role of Abrasive Blasting
Before a protective coating can do its job, it must be applied to a properly prepared surface. This is where surface preparation—particularly abrasive blasting—plays a pivotal role in corrosion control.
Abrasive blasting is one of the most efficient and effective ways to remove rust, mill scale, old coatings and other surface contaminants. It also creates the necessary surface profile (or “roughness”) that allows the coating to bond properly to the metal. Without this anchor pattern, coatings are more likely to delaminate or blister—leading to premature corrosion and costly maintenance.
Why Garnet is the Preferred Abrasive
There are several types of abrasives used in blasting, including coal slag, copper slag, and silica sand. But garnet stands out as the preferred choice for professionals focused on quality, safety, and long-term performance.
Garnet abrasives offer several key advantages:
- High performance: Garnet is a hard, durable mineral that cuts quickly and consistently—reducing blasting time and abrasive consumption.
- Cleaner surfaces: It produces minimal dust and leaves less embedment compared to slags, helping ensure the surface is truly clean for coating application.
- Low dust for safer work environments: Lower airborne particles support better operator visibility and health outcomes.
- Recyclability: High-quality garnet like GMA Garnet™ can be reused multiple times, making it more cost-effective and sustainable.
- Consistent results: GMA Garnet™ products are processed to tight specifications, helping deliver repeatable surface profiles for reliable coating performance.
PremiumBlast™ for corrosion protection project
Corrosion Protection Starts at the Surface
Corrosion is an inevitable challenge across heavy industries but with the right approach, its impact can be significantly reduced. Protective coatings remain one of the most effective tools for corrosion control, but their success depends on one critical foundation: proper surface preparation.
Abrasive blasting, especially when performed with high-quality abrasives like GMA Garnet™, plays a vital role in ensuring surfaces are clean, profiled, and ready for coating. By delivering consistent performance, low dust, and recyclability, garnet abrasives help prevent coating failures, extend asset life, and reduce the long-term costs of corrosion. Investing in the right surface preparation solution isn’t just about finishing the job—it’s about protecting it for years to come.