You’re currently viewing the Americas website.

You’re currently viewing the Americas website.
Would you like to switch countries or language?Blast Abrasives
Topics
Waterjet Cutting
Topics
Resources
Categories
Types
Categories
Topics
Abrasive Blasting Tech Tips English Global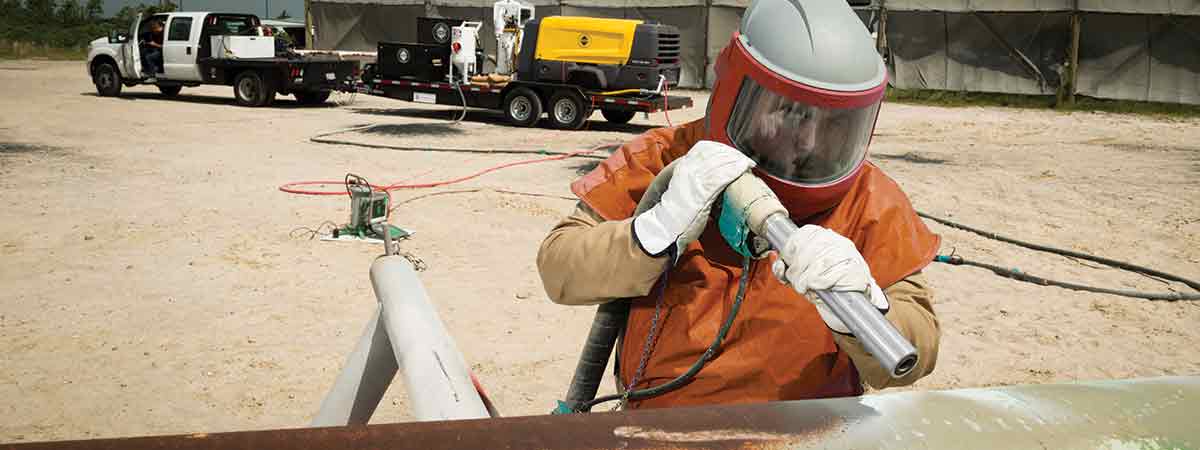
Advantages of finer grade garnet (Part III)
In this final series on finer grade garnet, we continue to explore the different and applications while highlighting three practical considerations in your blasting projects.
Fibreglass
Repairs to fibreglass surfaces often require removal of top layers of resin without causing damage to the gel coat. Smaller garnet grains will facilitate controlled surface preparation, localised repairs and create the desired feathering effect onto the intact resin.
Graffiti removal
The removal of graffiti will often need to be repeated on regular occasions. Hence, the facility to do the job without undue damage to the substrate is invaluable. The use of a finer grain garnet gives the blaster greater control and helps wear away unwanted decoration without ripping into the surface.
Turbines and propellers
Even the finest grade of garnet remains a hard and sharp tool. When turbines and propellers become encrusted with detritus, ultra-fine garnet at controlled pressures can be used for brush blasting without affecting the dynamics of the work piece.
Cases when finer garnet grains may not be appropriate
The range of particle sizes available within different grades garnets and the garnet performing at variable pressures combine to achieve a variety of finishes according to specific requirements. However, garnet performance is determined by the virtue of energy produced by velocity.
When removing thick soft coatings, the energy may be absorbed before the garnet grains achieve full impact potential. Hence, the heavier features of larger grain garnet can be more effective. Equally, when blasting off high build coatings above 500 microns in thickness and heavy corrosion on ships hulls, finer garnet grains may not be appropriate.
PRACTICAL CONSIDERATIONS:
- Optimal blasting performance is achieved by matching the correct garnet grain size for the specific job with clean, dry compressed air at the appropriate pressure in conjunction with controlled abrasive flow rates.
- Efficient paint application can be facilitated having a uniform surface profile and without rogue peaks or oversized troughs.
- The unique physical nature of garnet being sharp, hard and tough allows usage at lower air pressures, avoiding over blasting or unnecessary damage to the substrate.
CONCLUSION
The physical nature of finer grade garnet facilitates better blasting performance. Finer garnet grades can enable more controlled blasting, more efficient blasting performance and cleaner surface profiles up to 75 microns.
Certain surface coatings like mill scale, light rust and low build coatings can be removed more effectively with finer than coarser grade garnet.
Specialised finishes on applications like graffiti removal, fibreglass and flash blasting are made possible by the combination of finer grains and variable air pressure. Selecting the smallest particle size required to achieve the desired result will reduce the need to paint over rogue peaks or fill oversized troughs within the surface profile.
It is important to consult a garnet expert in your planning stage of project to obtain the right garnet abrasive for your desired profile. This can result in increasing blasting rates by more than 10% and reducing the volume of abrasive used by up to 10%, resulting in shorter project times and
lower cost.