You’re currently viewing the Americas website.

You’re currently viewing the Americas website.
Would you like to switch countries or language?Blast Abrasives
Topics
Waterjet Cutting
Topics
Resources
Categories
Types
Categories
Topics
Abrasive Blasting Our Customers English Global Projects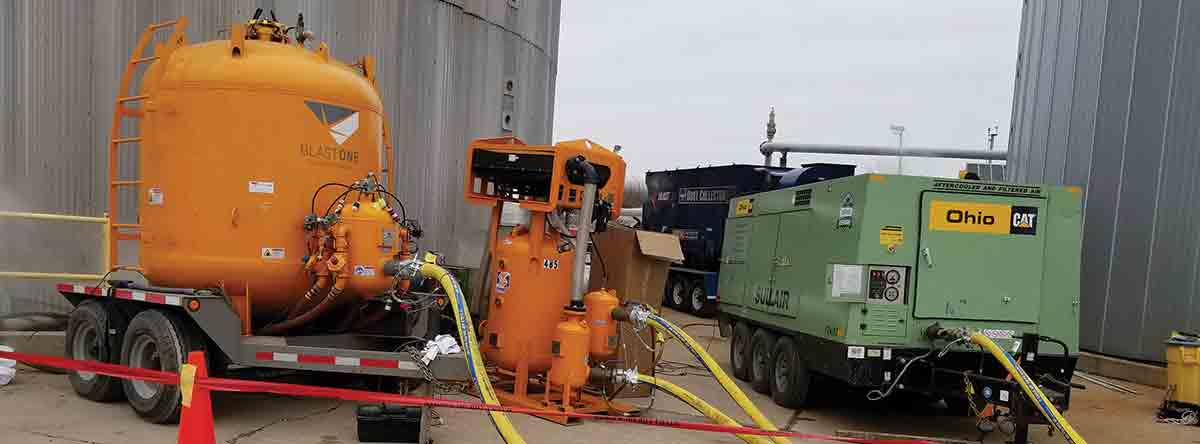
Blasting maintenance at BP-Husky refinery completes at half the time and cost
Concerned about the costs of compliance, risks posed by OSHA regulation and the time it was taking for work to get done on their sites; Contractor Advanced Industrial Services worked with BlastOne International to develop a cost-efficient blasting solution for an internal 14-metre (48-foot) diameter tank at the BP-Husky Toledo refinery.
The tank had some weldment repairs on the floor including new floor patches. The existing coating on the new steel patches was to be fully blasted and feathered into an existing 30 mils of sound coating.
The underside of the tank roof comprised of the flat section of the roof and panels. Both had a very thin coating with a significant amount of rust coming off in large sheets. The roof support beams were in sound condition, consisting of steel sectioned C-channels with a very thick 30 to 40 mil coating.
AIS estimated that they would require a truckload of slag - approximately eight to 10 bulk bags with at least a minimum of seven bags; and takes up to four days to complete. However, BlastOne is confident that GMA ToughBlast™ garnet abrasives can get the job done faster with less abrasive consumption. This alternative abrasive from GMA was put to the test.
While blasting on the floor patches, the blasters experienced a significant increase in speed and noted that the edges feathered in much quicker. They couldn’t believe how little dust there was.
When it came to blasting the roof, the blasters were blown away by the incredible speed of how quickly they could move the nozzle and remove the coating. The steel beams with sound coating were effectively cleaned without having to completely re-blast these.
The project was completed within one and a half days of actual blasting time and over two bags of GMA ToughBlast™ were consumed. This was less than half the amount of slag originally estimated!
In addition to the overall project cost reduction, switching to GMA ToughBlast™ has also helped the refinery reduce its green space (landfill) and remain in compliance with OSHA Beryllium regulations.
By Jim Gooden, BlastOne International.