You’re currently viewing the Americas website.

You’re currently viewing the Americas website.
Would you like to switch countries or language?Blast Abrasives
Topics
Waterjet Cutting
Topics
Resources
Categories
Types
Categories
Topics
Abrasive Blasting Tech Tips English Global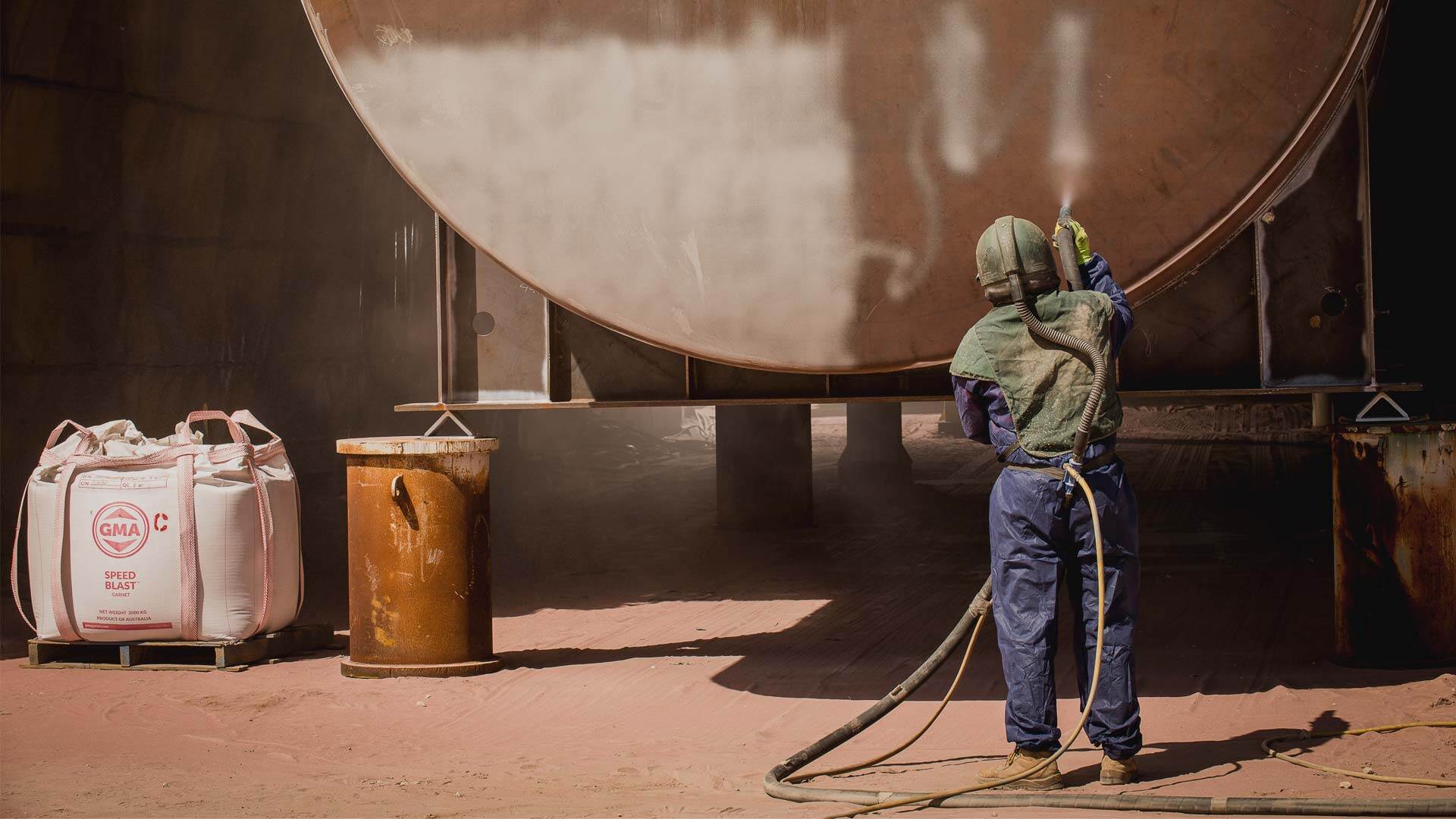
A Side-by-Side Comparison of Slag and Garnet Abrasives
When it comes to paint jobs, surface preparation often takes a back seat to the coating itself. However, the choice of abrasive used during surface preparation is far more critical than many realize.
From speed and safety to dust control and disruption, the abrasive you choose doesn't just affect the quality of the coating—it also has a direct impact on your facility's productivity and profitability. The right abrasive can significantly reduce downtime, while a poor-quality abrasive can cause unnecessary delays.
Waste slag has long been the go-to blasting abrasive. But new OSHA regulations and a shift toward fixed-price bidding have maintenance teams searching for a safer, more productive abrasive. While metallic abrasives and aluminum oxides are efficient, their price tags don't make them viable for general maintenance. Garnet's balance of affordability and quality has made it a top choice for industrial teams seeking safer, more productive abrasive blasting.
Should you use waste slag or garnet abrasives for surface preparation?
Blasting abrasives might not be at the top of your priority list, but they could be the secret to breaking through your 98.5% uptime plateau. If your blasters are using waste slag, use this side-by-side comparison to ensure you're making the best choice for your facility and your coatings job.
Blasting abrasives might not always be top of mind, but they could be the key to overcoming productivity challenges. If your team is still using waste slag, it's worth considering the benefits of switching to garnet. Here’s a side-by-side comparison to help you make the best decision for your facility.
Performance
Your blasting abrasive must produce the surface profile required by your industrial coating. Toughness, hardness and density all directly impact an abrasive's ability to perform the task. The harder the abrasive, the more effectively it removes tough coatings and creates an anchoring profile. The tougher the abrasive, the less likely it is to shatter upon impact. Tougher abrasives produce a higher surface profile faster. Density affects productivity by enabling a deeper anchor pattern.
TIP: Garnet abrasives produce a cleaner surface, faster than waste slags, keeping turnaround timelines on schedule.
Consumption
The amount of abrasive you need to achieve the desired surface preparation is critical to the overall cost of your job. Consumption can also cause productivity killers such as lengthy disposal processes and dust. (The latter of which is so critical that we've devoted a separate section to it below.)
TIP: Maintenance teams can reduce consumption by 30% to 50% by switching from waste slags to garnet abrasives. By getting the job done with less, teams also reduce disposal and cleanup, allowing a facility to get back to productivity faster.
Dust
For many maintenance managers, dust has become such an issue that it's standard practice to take other trades off their jobs as blasters do theirs. Although no abrasive blasting is truly dust-free, your choice of abrasive has a drastic impact on dust and disruption in your facility. Simply put, more consumption means more dust.
TIP: Garnet is the closest thing to dustless blasting. Because of its inherent toughness, it causes less dust, contamination and facility disruption than waste slag.
Heavy Metals and Toxicity
You can't eliminate abrasive blasting altogether, but you can choose abrasives that pose less safety risk. In addition to dust and contamination, toxicity is key to assessing the quality of your blasting abrasive.
TIP: Garnet is within OSHA's limits for beryllium and doesn't contain the toxic heavy metals found in waste slags. By blasting with garnet, maintenance teams can maximize safety without sacrificing performance.
Cost
It's tempting to think of abrasive costs in terms of material alone. But speed, cleanup and disruption all factor into a blasting abrasive's affordability (or lack thereof).
TIP: Whether recycled or used just once, garnet's speed, efficiency and lower disposal costs make it a cost-effective abrasive.
The Bottom Line
In today’s fast-paced industrial environment, there’s no room for waste slag’s dust, disruption, and downtime. That’s why maintenance teams worldwide are turning to GMA Garnet™ to get the job done right. Let's discuss how garnet abrasives can help your facility maximize uptime and efficiency on your next coatings project.
Read the complete guide