You’re currently viewing the Global website.

You’re currently viewing the Global website.
Would you like to switch countries or language?Product Range
Tools & Resources
Featured products
Tools & Resources
Featured products
Tools & Resources
Resources
Categories
Types
Categories
Topics
Waterjet Cutting Case Studies Global All Languages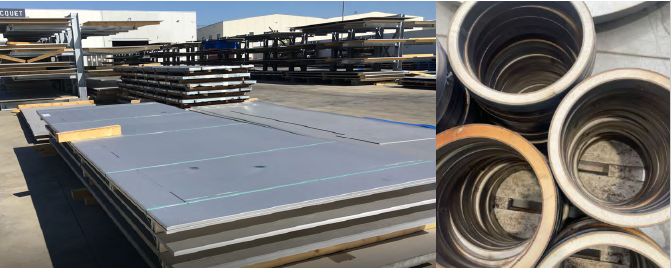
Comparative Study of Waterjet vs. Laser Cutting for Stainless Steel
Overview
Project
Jacquet Nova Srl conducted a comparative study to evaluate the cutting quality of waterjet versus laser cutting technologies on a 40mm-thick AISI 304 stainless steel part, known for its corrosion resistance and durability. This test aimed to identify the best technology for producing high-quality metal parts.
Location
Milan, Italy
Challenge
Jacquet Nova Srl experienced quality issues with laser cutting AISI 304stainless steel, leading to material defects like heat-affected zones and deformations, critical for precision-required industries
Company Overview
Founded in 2001 in Italy, Jacquet Nova Srl is a leading distributor of AISI 304 stainless steel and nickel alloys. The company specializes in supplying metal parts, sheets, plates, bars, and tubes cut to size for the construction industry. Operating globally, Jacquet Nova Srl stocks a wide array of CNC cutting machines, including plasma, laser, saw, and waterjet systems, to achieve high-quality finishes, tight tolerances, and fast deliveries.
Problem
While laser cutters provided speed, they often altered the mechanical and chemical properties of AISI 304 stainless steel, leading to heat-affected zones (HAZs), oxide inclusions, and material deformation. These issues compromised the part’s quality and suitability for precision-required industries.
Confidence in every cut
Solution
The company employed a 4,000 bar (60,000 psi) waterjet cutting machine, utilizing GMA Garnet™ for enhanced edge qualities. This method was chosen to avoid heat-induced damage and to maintain the integrity of the stainless steel during cutting.
Results and Industry Implications
The waterjet cutting produced a part with a smoother finish, no scorch marks, and less tapering compared to the laser-cut part, which showed significant HAZs, oxide inclusions, and deformation. The superior
quality of the waterjet cut demonstrated its reliability and raised concerns about the use of laser cutting for applications that demand high precision and corrosion resistance.
Future Plans
Jacquet Nova Srl, encouraged by the positive outcomes of the waterjet versus laser cutting comparison, is planning to expand its use of waterjet technology. This decision is driven by the need in industries like aviation and architecture for precise, corrosion-resistant parts free from HAZs or oxide inclusions. While acknowledging the speed benefits of laser cutting, Jacquet Nova Srl is committed to maintaining a balance between speed, precision, and quality. The company’s focus on expanding waterjet usage underscores their commitment to upholding high-quality standards and improving the quality of their products, reflecting a broader industry trend towards prioritizing cut quality in critical applications.