You’re currently viewing the Global website.

You’re currently viewing the Global website.
Would you like to switch countries or language?Product Range
Tools & Resources
Featured products
Tools & Resources
Featured products
Tools & Resources
Resources
Categories
Types
Categories
Topics
Abrasive Blasting Tech Tips Australia All Languages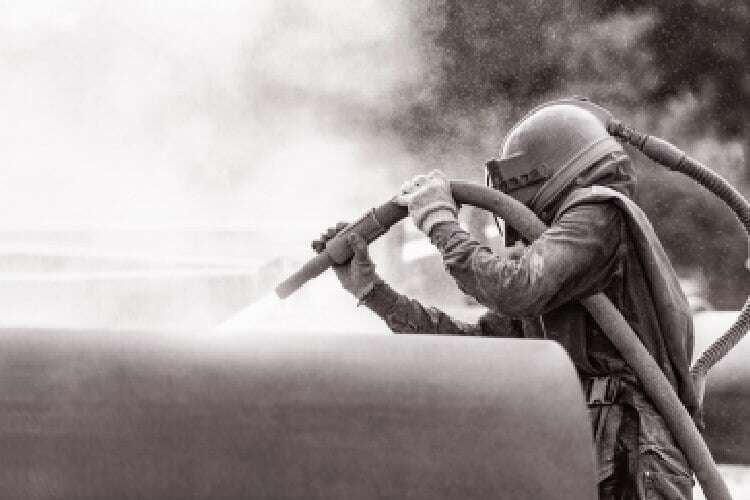
Understanding Australia's Silica Limits in Abrasive Blasting
Did you know? Over 587,000 Australian workers were exposed to silica dust in 2011. Across construction sites, shipping yards, even the home renovation project, exposure to silica dust can cause severe adverse health effects, including silicosis and lung cancer. A risk no worker should have to take.
So where does silica come from? Silica is a naturally occurring mineral that is commonly found in sand, rock, and soil.
When silica is used as an abrasive material, it can become airborne in the form of respirable crystalline silica (RCS) particles, which are small enough to be inhaled into the lungs.
The levels of silica in abrasive blasting can vary depending on several factors, including the type of abrasive material used, the blasting equipment and techniques, and the duration and frequency of the blasting process. In general, the levels of silica in abrasive blasting can be high, particularly if proper safety measures are not taken.
Australia’s 2020 change to the silica limit
A health-based review of the current scientific evidence for silica dust showed that the Workplace Exposure Standard (WES) should be reduced to prevent adverse health effects such as silicosis and lung cancer in workers.
Triggered by the increase of synthetic stone tops (leading to a spike in health- related cases and silica dust exposure), it has been found that the synthetic material has a higher concentration of dangerous particles compared to natural stones like marble. As a result, the Australian government has tightened its controls, aiming to reduce 30% of serious silica dust related serious injuries and illnesses.
What does this mean for your abrasive blasting operations?
In 2020, Safework Australia released an updated code of practice, placing duty of care of those who have a role in managing the risks of abrasive blasting. From designers, manufacturers and suppliers to company directors and contractors, all have a duty of care for their own, their workers, and any others health and safety on site.
Free crystalline silica - Concentration in the bag and the air
The Standards state that:
- Materials with more than 1%* free crystalline silica should not be used for abrasive blasting. *GMA takes reference from ISO 11126-10:2017, SSPC- AB1 (NIOSH Method 7500)3 that outlines the latest free crystalline silica limits.
- Respirable crystalline silica (silica dust) limits have changed from 0.1 mg/m3 to 0.05 mg/m3.
Compliance with the WES is required under the Commonwealth, state and territory Work Health and Safety (WHS) laws. This means that workers should not be exposed to more than 0.05mg/ m3 silica dust over an eight-hour working day, for a five-day work week.
Not all abrasives are created the same.
The quality levels of garnet depend on the deposit, mining, and processing controls in place. Through GMA’s world-class mining and processing procedures, the free quartz and other waste materials are almost completely removed. Samples are taken every two hours to ensure GMA’s processed garnet abrasives are of the highest standards.
GMA’s free crystalline silica results come well under the minimum threshold of 1% of weight by volume (usually under 0.1%), unlike other garnet suppliers. (Refer to graph compiled from independent laboratory test reports).
GMA Garnet™ is not only intrinsically safe to use, its consistent sizing and quality produce reliable abrasive blasting performance every time. Garnet is systematically tested and analyzed across 12 key areas, ensuring that GMA Garnet™ meets the highest industry, safety, and quality standards.
It is important to check in with your local WHS regulator to see if they have introduced any new regulations for silica dust and any other airborne contaminants.
*WES https://engage.swa.gov.au/wes-review-release-5
Minimize the risk
To minimize the risk of silica exposure during abrasive blasting, it is important to follow the recommended safety guidelines and regulations.
These may include:
- Using alternative abrasive materials that are less hazardous, such as garnet, aluminum oxide, or crushed glass.
- Using appropriate blasting equipment, such as a ventilated blasting cabinet or a blast room with proper ventilation systems.
- Using personal protective equipment (PPE), such as a respirator, gloves, and eye protection.
- Limiting the duration and frequency of the blasting process.
- Conducting regular air monitoring to measure the levels of silica in the air.
By following these guidelines and regulations, it is possible to minimize the risk of silica exposure during abrasive blasting and ensure the health and safety of workers and others in the vicinity of the blasting process.
To find out more, download our eBook Understanding Australia’s Silica Limits.
By Chris Manger
GMA Sales Manager Australia/Pacific