Achieve the cleanest, most consistent surface
A visual inspection only reveals part of the picture. GMA Garnet™ ensures a cleaner, more consistent surface that outperforms slag abrasives and prolongs coating life.
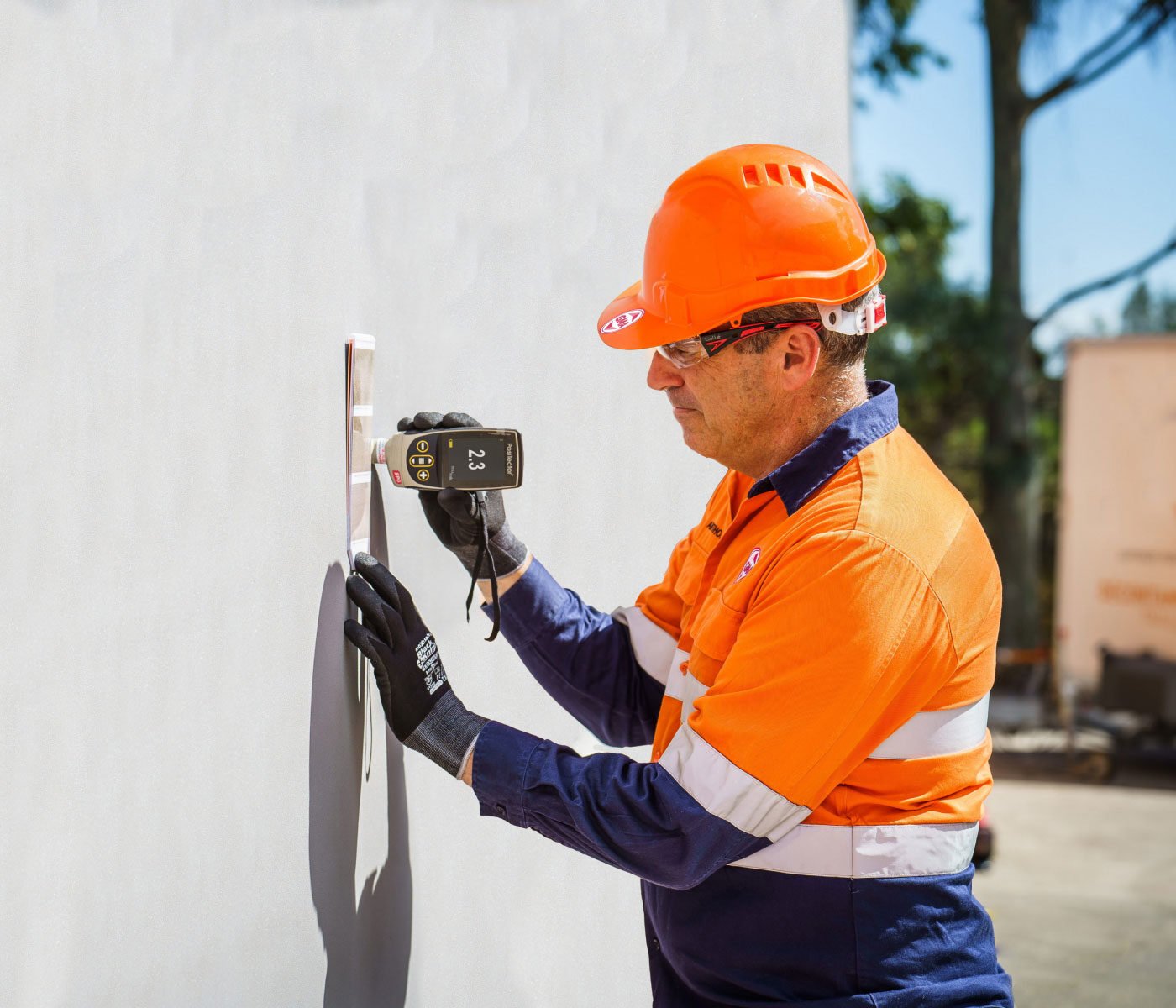
Minimizing embedment for extended coating life
When using slag abrasives, 60% of a surface on average will have embedment (abrasive particles stuck to the substrate). This unwanted foreign material can cause corrosion and blistering, leading to high rework costs or potential warranty claims. Coatings are designed to adhere to the substrate material, not the abrasive material, which further risks coating failure.
GMA Garnet™ is a remarkably tough natural mineral, up to 500% tougher than coal slags. It is far more resistant to fracturing on impact with a substrate than other abrasives, leaving minimal embedment on the surface. By reducing embedment, GMA Garnet™ enhances adhesion and extends coating life.
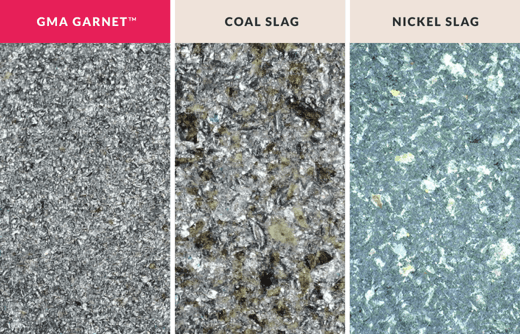
Image under magnification
Uniformity is key to coating adhesion and longevity
Achieving a consistent surface profile not only reduces overall labor and material costs, but also allows coatings to work optimally. A surface with few extreme peaks and valleys requires less primer — the foundation for coatings — to meet a coating specification. Slag abrasives produce an inconsistent pattern, requiring a thicker coat of primer for even coverage.
Maximizing coating adhesion with peak density
Peak density, the number of peaks and valleys per square inch produced by abrasive blasting, is crucial for coating adhesion. A higher peak density creates more surface area on the blasted substrate, enabling significantly better coating adhesion. While many products can produce the required surface profile, the extent and consistency of the substrate achieving this profile varies.
Our uniquely tough GMA Garnet™ engineered blends can generate up to 400% higher peak density than slag abrasives, resulting in measurably higher coating adhesion and surface integrity.
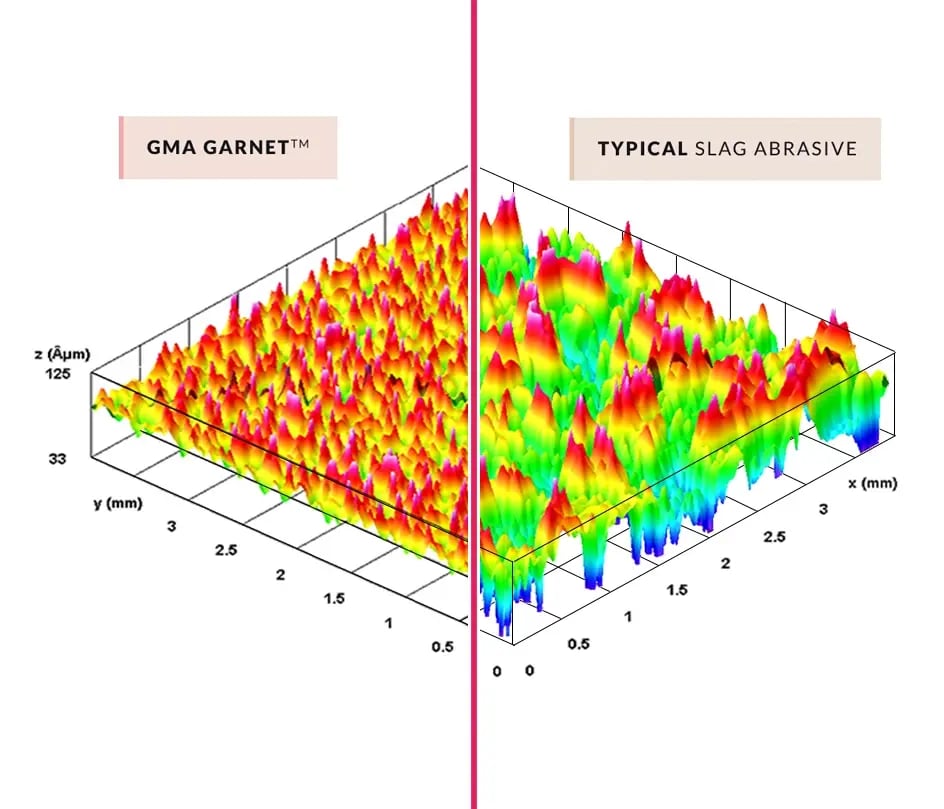
Lorem ipsum dolor sit
How GMA Garnet™ abrasives work
Tough, dense garnet
The unique natural hardness, toughness, density, and angularity of GMA Garnet™, combined with our processing methods refined over 40 years, produce exceptionally clean, consistent surfaces.
Engineered blends
GMA’s innovative range of abrasives contain coarse and fine garnet grains, optimally balanced for strong cutting power and cleaner surfaces in specific blast applications.
Unmatched reliability
The consistent sizing and purity of GMA Garnet™ enable operational efficiency, with every bag delivering an abrasive that performs to the highest standards.
Quality assurance
Regular sizing and QA/QC of GMA Garnet™ in 12 areas of performance ensures zero out-of-spec particles, allowing precise blasting that avoids costly rework.
Frequently asked questions
Don’t overlook the importance of your choice of abrasive in surface preparation. For more information on switching to GMA Garnet™, visit the FAQs library.
Why should I focus on surface preparation in my project?
Focusing on surface preparation is crucial for the success of your project for several reasons:
Preventing coating failures: It is estimated that up to 80% of coating failures are due to inadequate surface preparation. Proper surface preparation ensures the substrate is clean, dry, and properly profiled, which is essential for effective coating adhesion. Contaminants must be properly removed.
Cost efficiency: Although surface preparation can represent 30% to 60% of the total project cost, this investment is crucial for long-term savings. Proper surface preparation enhances coating performance and longevity, reducing the need for costly repairs and maintenance down the line.
Improved coating longevity: Effective surface preparation ensures that coatings adhere well and function as intended, leading to extended maintenance schedules and better overall coating durability. This not only saves money over time but also enhances the reliability and performance of the coated structure.
The specification asks for a certain profile height and preparation technique. I can't change this specification now. What should I do?
You can work with the asset owner or engineering firm if you have some concerns. Get GMA involved and consider conducting different testing protocols with your abrasive supplier and coating manufacturer. Our technical team can assist in adjusting equipment settings and optimizing blasting techniques to ensure that GMA Garnet™ meets the required specifications.
Additionally, using GMA Garnet™ can contribute to better coating longevity and extended maintenance schedules, which saves money over time. By bringing innovative solutions to the table, you will be seen as a contractor or supplier of choice, enhancing your reputation and customer satisfaction. Speak with a GMA expert.
I can achieve the surface profile required with cheaper abrasives. Why should I use GMA Garnet™ and get the same result?
GMA abrasives give a much higher degree of control over the surface profile produced, reducing the risk of going over or under specification and requiring rework. You will also achieve a much more consistent surface profile with more surface area achieving the specified profile. This results in better coating adhesion and lifespan and reduces the possibility of coating failure and warranty claims.
I’ve never had a surface preparation failure from using a slag abrasive before, so why should I change now?
While slag abrasives may have worked adequately for your needs in the past, switching to GMA Garnet™ can offer several compelling benefits that enhance your overall blasting efficiency and effectiveness:
Superior performance: GMA Garnet provides a more consistent surface profile and higher quality finish due to its uniform particle size and superior hardness. This can improve the adhesion of coatings and the longevity of the treated surfaces.
Health and safety: GMA Garnet generates significantly less dust compared to slag abrasives, improving visibility, reducing respiratory hazards for operators, and contributing to a cleaner work environment.
Cost savings: The lower consumption rates, reduced downtime for abrasive replenishment, and decreased cleanup costs translate to substantial overall cost savings. Additionally, less wear and tear on equipment due to lower dust levels and more efficient blasting leads to lower maintenance and replacement costs.
Speak to your local GMA Garnet™ expert
Lorem ipsum dolor sit
Donec consequat dolor vulputate enim rhoncus, non maximus ligula venenatis?
Lorem ipsum dolor sit amet, consectetur adipiscing elit. Donec eget maximus sem. Suspendisse eget felis dolor. Lorem ipsum dolor sit amet, consectetur adipiscing elit. Nam egestas justo vitae tempus interdum. Etiam blandit et lectus non malesuada.
Sed lacinia ex id risus scelerisque fermentum. Praesent tellus tortor, placerat vitae nulla a, fringilla rutrum ex. Nunc semper et risus sed convallis. Morbi sollicitudin aliquam felis a faucibus. Nullam ut dictum elit, et feugiat elit.
Nunc nec arcu eget lectus dapibus congue sed a lorem nec est scelerisque faucibus?
Lorem ipsum dolor sit amet, consectetur adipiscing elit. Donec eget maximus sem. Suspendisse eget felis dolor. Lorem ipsum dolor sit amet, consectetur adipiscing elit. Nam egestas justo vitae tempus interdum. Etiam blandit et lectus non malesuada.
Sed lacinia ex id risus scelerisque fermentum. Praesent tellus tortor, placerat vitae nulla a, fringilla rutrum ex. Nunc semper et risus sed convallis. Morbi sollicitudin aliquam felis a faucibus. Nullam ut dictum elit, et feugiat elit.
Arcu eget lectus dapibus congue?
Lorem ipsum dolor sit amet, consectetur adipiscing elit. Donec eget maximus sem. Suspendisse eget felis dolor. Lorem ipsum dolor sit amet, consectetur adipiscing elit. Nam egestas justo vitae tempus interdum. Etiam blandit et lectus non malesuada.
Sed lacinia ex id risus scelerisque fermentum. Praesent tellus tortor, placerat vitae nulla a, fringilla rutrum ex. Nunc semper et risus sed convallis. Morbi sollicitudin aliquam felis a faucibus. Nullam ut dictum elit, et feugiat elit.
Nunc nec arcu eget lectus dapibus congue sed a lorem nec est scelerisque faucibus?
Lorem ipsum dolor sit amet, consectetur adipiscing elit. Donec eget maximus sem. Suspendisse eget felis dolor. Lorem ipsum dolor sit amet, consectetur adipiscing elit. Nam egestas justo vitae tempus interdum. Etiam blandit et lectus non malesuada.
Sed lacinia ex id risus scelerisque fermentum. Praesent tellus tortor, placerat vitae nulla a, fringilla rutrum ex. Nunc semper et risus sed convallis. Morbi sollicitudin aliquam felis a faucibus. Nullam ut dictum elit, et feugiat elit.